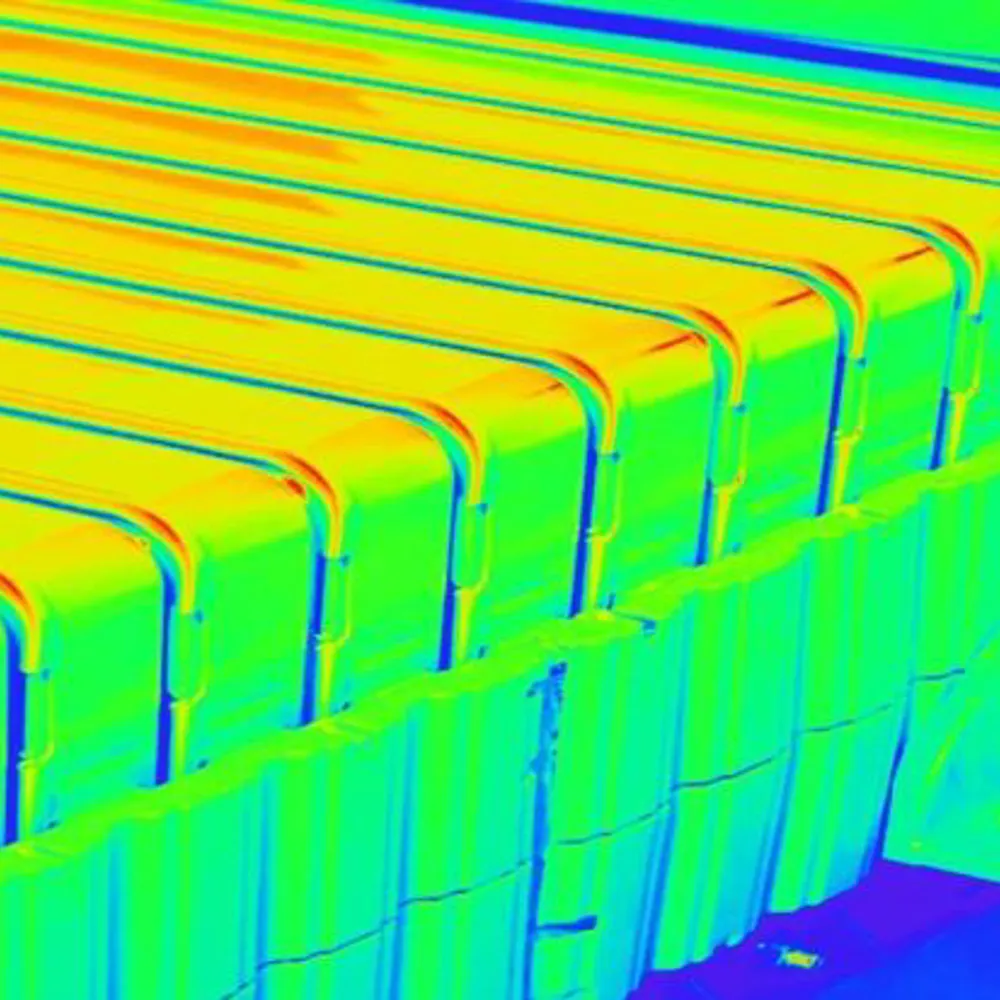
Electric Vehicle Battery Thermal Management Solutions
As a world-class converter and precision die-cutting expert, JBC Technologies has the knowledge and experience required to fabricate custom laminated and die-cut EV battery thermal management solutions that meet your exact specifications. Whether you need a single material with an adhesive backing or a complex multi-layer laminate die-cut to shape, we will deliver the high-quality results you need.
Have an EV battery thermal management challenge?
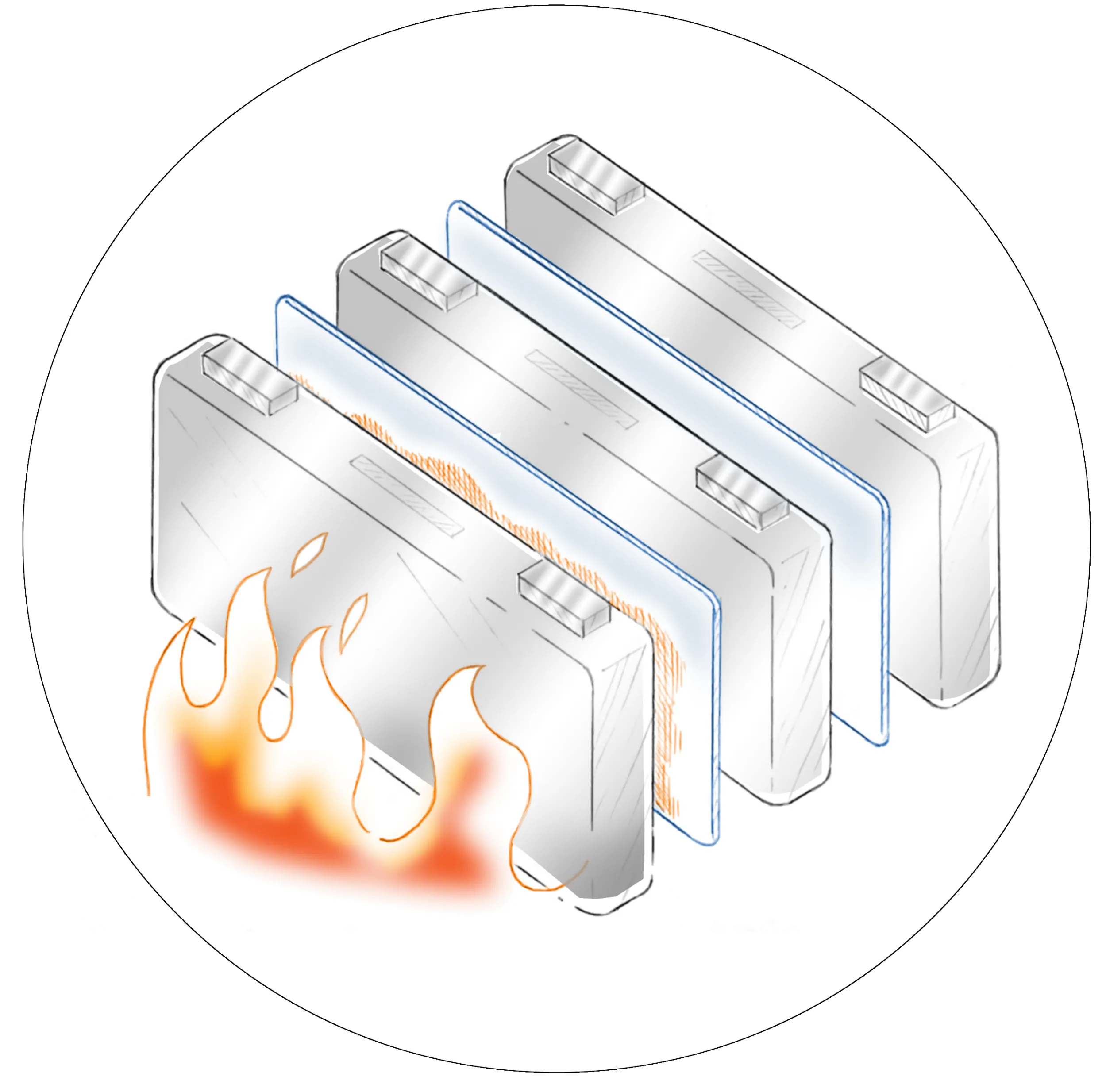
Thermal management Applications for Precision Die-Cut Solutions
Custom die-cut parts are versatile, cost-effective solutions for addressing EV battery thermal management challenges.
From thermal gap fillers to cooling channel gaskets, each application plays a unique role in optimizing the thermal performance of EV batteries. Several applications for custom die-cut components that target EV battery thermal management include:
- Heat shielding
- Ventilation seals
- Bus bar insulation
- Thermal gap filling
- Connector insulation
- Cooling channel gaskets
- Hot-spot heat spreading
- Cell-level insulation and isolation
- Pack -level insulation and isolation
- Module-level insulation and isolation
EV battery thermal management is crucial for optimal performance, safety, and longevity of electric vehicles. Overheating or overcooling of the battery cells can reduce their efficiency and lifespan, and even cause safety hazards

pERFORMANCE MATERIALS for ev battery thermal management
JBC Technologies is a leading provider of custom die-cut solutions for various industries, including electric vehicles (EVs). As the demand for EVs continues to rise, thermal management has become a critical concern for EV battery safety and performance.
The goal of insulation in EV battery thermal management is to minimize heat loss from the battery to the surrounding environment, and to prevent temperature imbalances between different parts of the battery. This can help to maintain battery performance and prolong battery life.
The goal of spreading in EV battery thermal management is to improve heat transfer between the battery cells and cooling systems. This can help to dissipate heat more effectively, and prevent hotspots that can lead to thermal runaway and safety hazards.
The goal of shielding in EV battery thermal management is to protect the battery from external heat sources or impacts that could cause damage or safety hazards. Shielding materials can also help to contain fires or other safety incidents within the battery system, reducing the risk of damage or injury to the vehicle or occupants.
Here are a few of the specialty materials available for your custom EV battery thermal management solutions
INSULATING
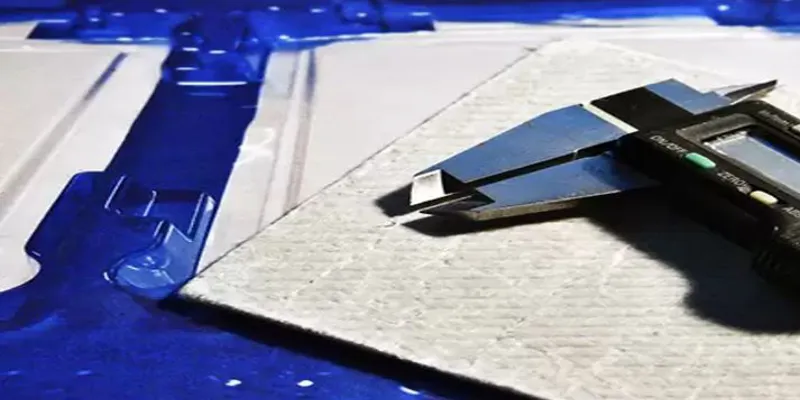
Aerogels
Aerogels are being used in EV battery thermal management as insulation materials between battery cells and outer packaging. Aerogels have advantages over other insulation materials due to their lightweight, thin, flexible nature, and extremely low thermal conductivity.
Example: PyroThin from Aspen Aerogels®
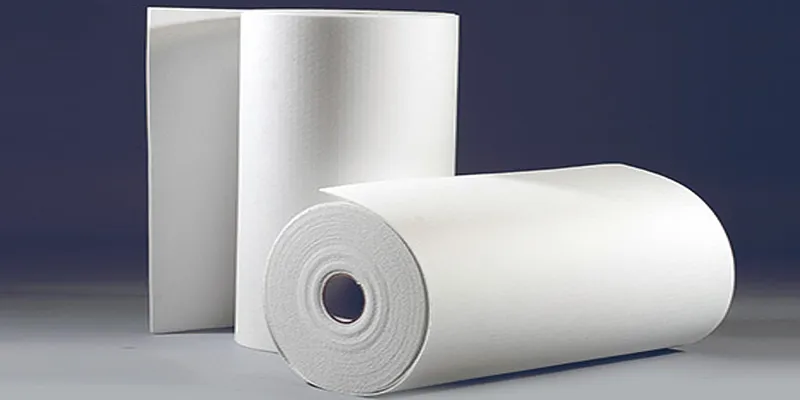
Ceramic Papers
Ceramic paper is being used in EV battery thermal management as an insulation material between battery cells and outer packaging. These papers have advantages such as high thermal stability, good mechanical properties, and low thermal conductivity, which makes them effective in providing excellent insulation while occupying minimal space.
Example: EST Compression Papers from Morgan Thermal Ceramics
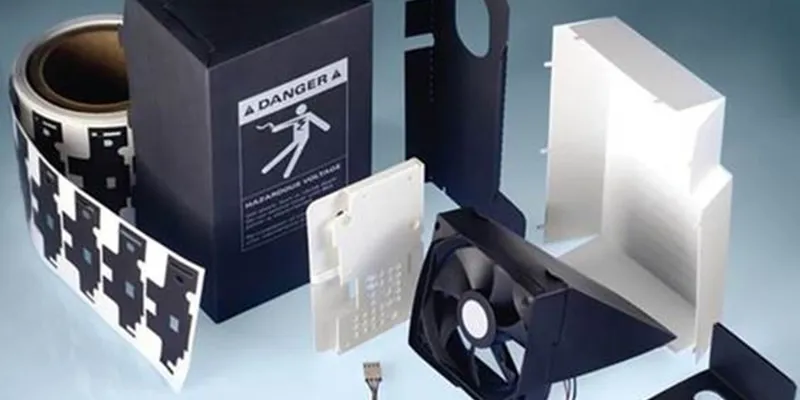
Polypropylene Sheets
Polypropylene sheets like Formex are being used as insulation materials in EV battery thermal management. They are lightweight, flexible, and flame-retardant, with good electrical insulation properties. While they may not have as high a thermal conductivity as other materials, they are cost-effective and readily available in a range of thicknesses and densities.
Example: Formex® GK flame retardant insulation from ITW
SPREADING
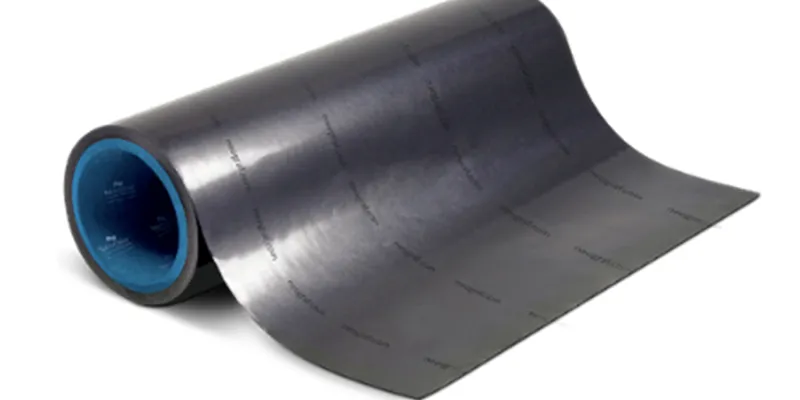
Flexible Graphite
Flexible graphite is being used in EV battery thermal management as a thermal interface material between the battery cells and the cooling system. It has advantages such as excellent thermal conductivity, good mechanical properties, and chemical inertness, and is relatively inexpensive compared to other high-performance TIMs.
Example: eGraf® Spreadershield™ from Neograf™ Solutions
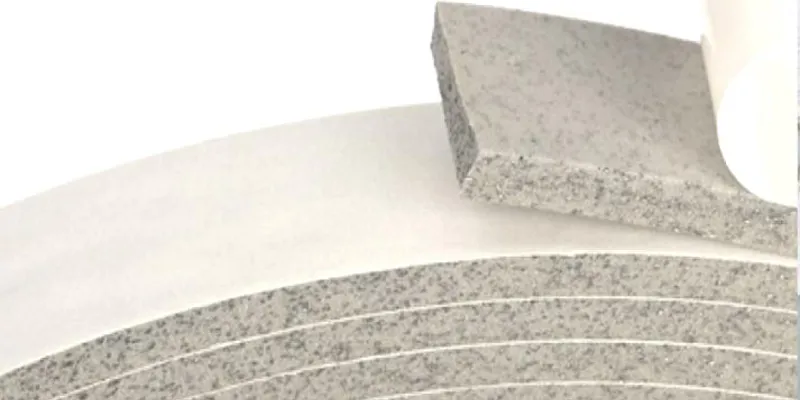
Phase Change/Intumescents
Phase change and intumescent materials are being used in EV battery thermal management as thermal management systems (TMS) to regulate the temperature of the battery cells. Phase change materials (PCMs) absorb and release heat during phase transitions, while intumescent materials (IMs) expand upon heating to form an insulating layer. Both types of materials can help to maintain the temperature of the battery pack within a desired range by absorbing and dissipating heat.
Example: Norseal® FS1000 intumescent foam from Saint-Gobain
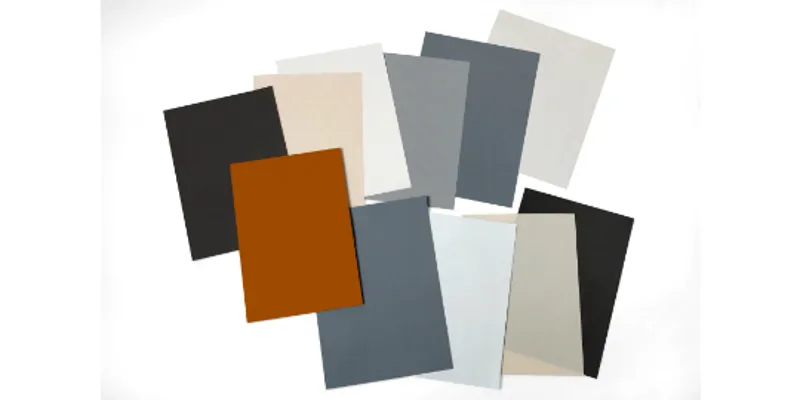
Gap Pads
Gap pads are being used in EV battery thermal management as thermal interface materials between battery cells and cooling systems. They are typically made from silicone or other elastomeric materials and are easy to install, flexible, non-conductive, and have a low thermal resistance. While they have some limitations, such as lower thermal conductivity and limited thermal stability at high temperatures, they are a promising solution for applications where space and weight are limited and where ease of installation and safety are important considerations.
Example: 5591 Thermally Conductive Silicone Interface Pad from 3M™
SHIELDING
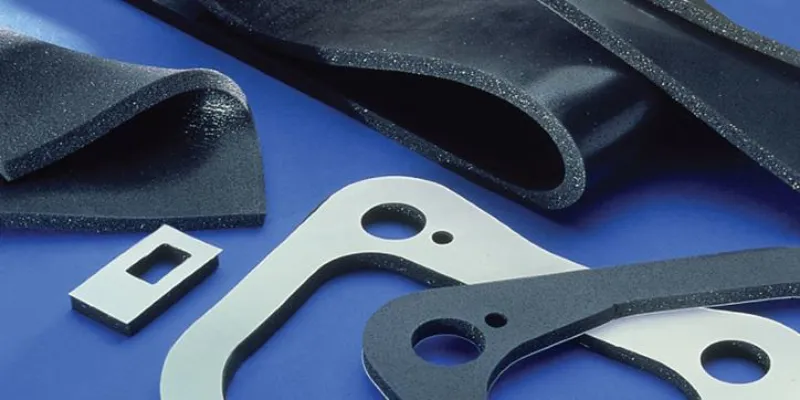
Microcellular Polyurethanes
Microcellular polyurethanes are being used in EV batteries as thermal interface materials (TIMs) for enhancing heat transfer between the cell and cooling system. These materials are lightweight, flexible, have high thermal conductivity and resilience, which makes them ideal for use in the complex geometries of EV batteries. They are a popular choice because they offer excellent compression set resistance and are available in various thicknesses and hardness levels.
Example: PORON EVExtend® battery pad material from Rogers Corporation

Micas
Mica is a mineral with good thermal conductivity and electrical insulation properties that can be used in EV battery thermal management. It can be used as an insulation material between battery cells and cooling systems, and as a thermal interface material to improve heat transfer. While mica-based TIMs have high thermal conductivity and stability, they can be brittle and may not be suitable for applications where space and weight are limited.
Example: EST™ M Paper from Morgan Thermal Ceramics
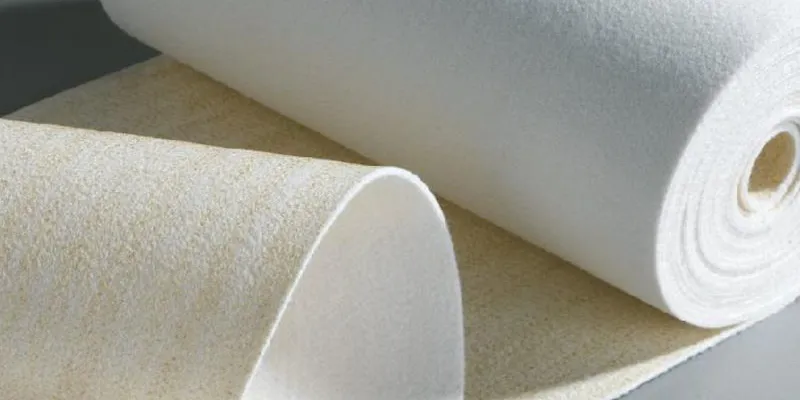
Polyamide Papers
Polyamide papers are thin, flexible, and heat-resistant materials commonly used as insulating materials in electrical applications. They are being evaluated as a promising material for use as separators in EV batteries, due to their high thermal stability, good mechanical properties, and low moisture absorption. However, extensive testing and evaluation are required to ensure that the battery meets the desired performance, safety, and reliability standards.
Example: Nomex® 410 papers from DuPont™
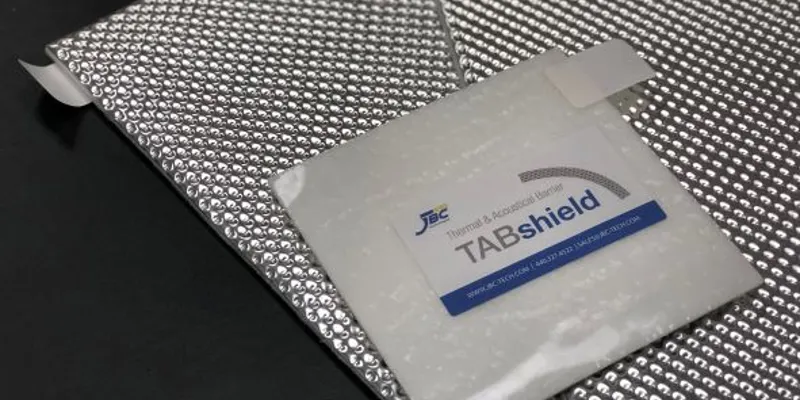
TABshield Thermal Barrier
This lightweight alternative to traditional metal heat shields is an easy-to-install, conformable solution for a variety of targeted EV noise and heat suppression applications. TABshield patches can be customized with pull tabs, peel-and-stick adhesive backing, embossing, and microperforating for improved acoustical performance.
Example: TABshield™ Thermal/Acoustical Barrier from JBC Technologies
The JBC Advantage For EV Battery Thermal Management
At JBC Technologies, we offer a range of unique advantages that set us apart from other solutions providers in the thermal management industry. We have strong relationships with some of the world's leading suppliers of thermal management materials, allowing us to identify and provide the right materials for your specific needs.
Using our vertically integrated converting capabilities, JBC combines specialty materials, each with its own performance attributes, into single, lightweight, economical, easily-installable components with multiple end-use contributions – and a single SKU!
We do this through
-
Part Presentation
-
Automated Assembly
-
And More
Contact us today to learn more about how we can help you achieve your goals.