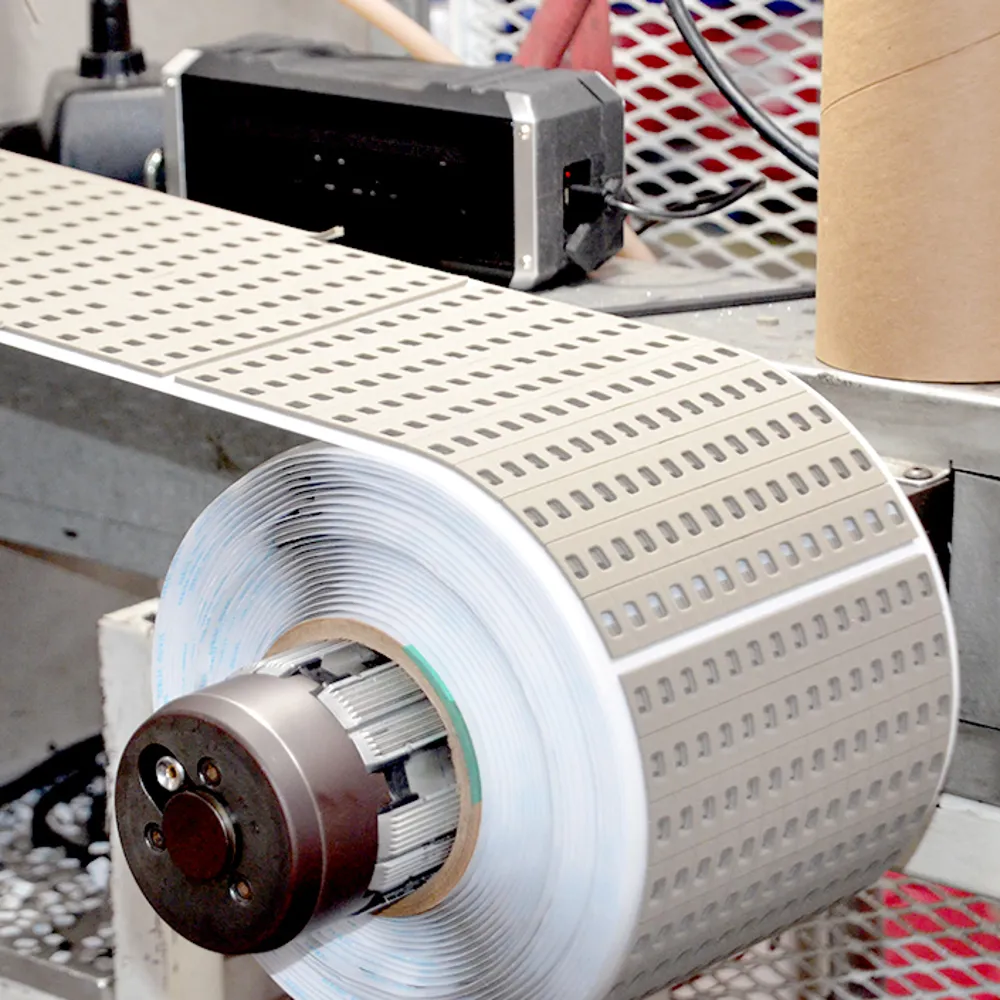
Precision Die-Cutting and Converting Capabilities
JBC Technologies is a premier flexible materials converter and die-cut manufacturer with four production facilities totaling over 150,000 square feet of manufacturing space. Industry-leading capabilities allow JBC to control cost, responsiveness, and quality throughout the die cutting process – from raw material to finished goods. JBC Technologies has the inventory capabilities and stock to offer fast turnaround times while maintaining competitive pricing.
With over 30 years of industry experience, JBC has the expertise and capabilities to deliver unparalleled customer service and die cut products. Click the button below to learn more.
Flexible Materials Converting & Die-Cutting SErvices
From custom die-cut parts and rapid prototyping services to supply chain management solutions, JBC offers a full range of innovative die-cutting and converting capabilities. We work with a wide range of flexible materials –offering custom manufacturing and engineering services, such as:

Precision Die-Cutting
Whether your die-cut parts require a straightforward steel rule manual die, a multi-step servo controlled matched progressive rotary system with integrated island placement, or anything in between, JBC has the solution. With over 30 years of experience, expert team members, and state-of-the-art equipment, we can handle all of your die-cutting needs.
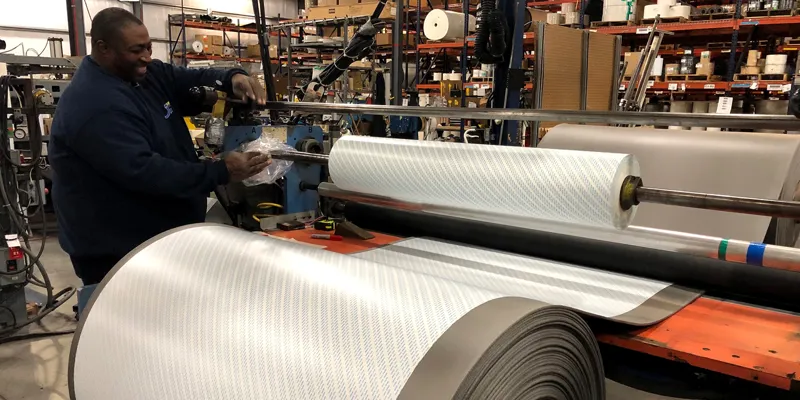
Flexible Materials Converting
JBC Technologies’ vertically integrated converting capabilities range from slitting and laminating to foam splitting, surface treating, wide-web embossing, and micro-perforating. We produce everything from prototypes to large volume runs in house. This allows us to transform materials from mill rolls to finished parts, keeping costs down and eliminating any potential supply chain risk for our customers.
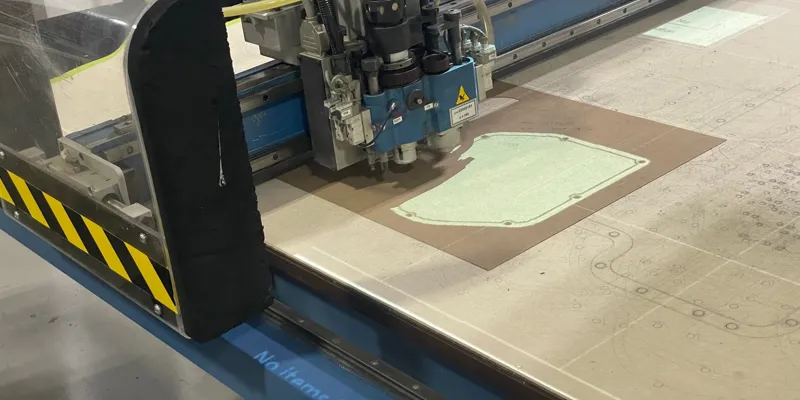
Dieless Digital Cutting
JBC’s digital die-cutting (dieless cutting) equipment not only expands the breadth of materials we can work with, but it also enables us to provide rapid response times to customers that are looking for prototypes or short production runs. If you are looking for die cut technologies in a hurry, digital die cutting might be the right choice for you.
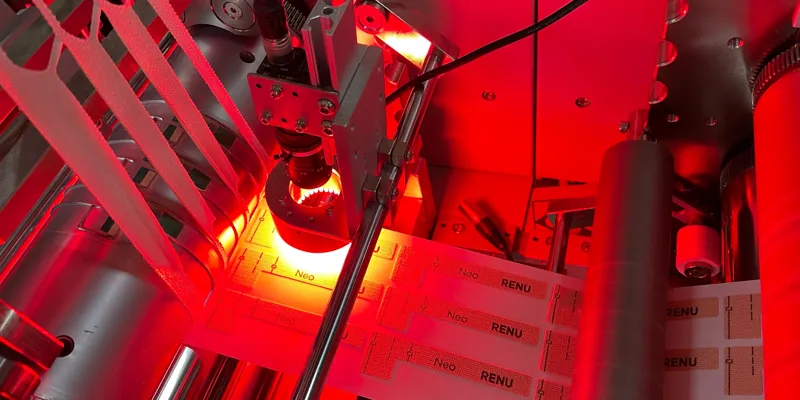
Class 8 Clean Room
JBC Technologies knows the importance of being able to offer clean room manufacturing capabilities to our customers. Our ISO 8 (Class 100,000) clean room environment encompasses every step of the manufacturing process. Using our state-of-the-art, high-speed 10-station DCS rotary die-cutting press, we can produce custom die-cut parts as well as inspect and package them all within the clean room area.
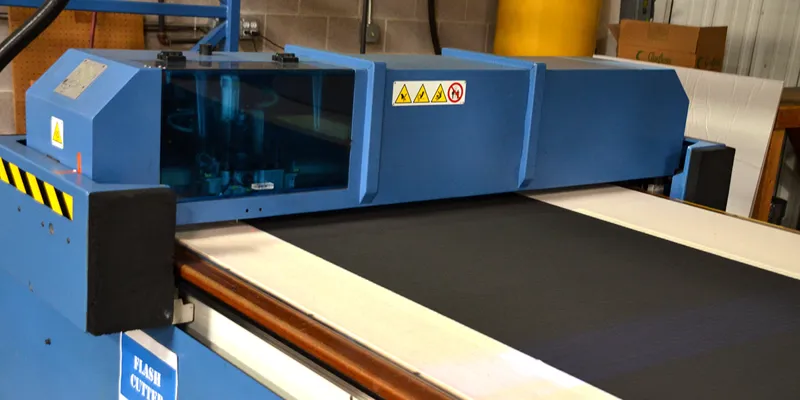
Rapid Prototyping
JBC’s digital precision cutting machines can quickly produce parts that would normally be die-cut, taking them from CAD drawing to finished part in seconds – with no tooling required. As a result, they are an excellent resource for design engineers looking to test different materials or validate proof of concept.
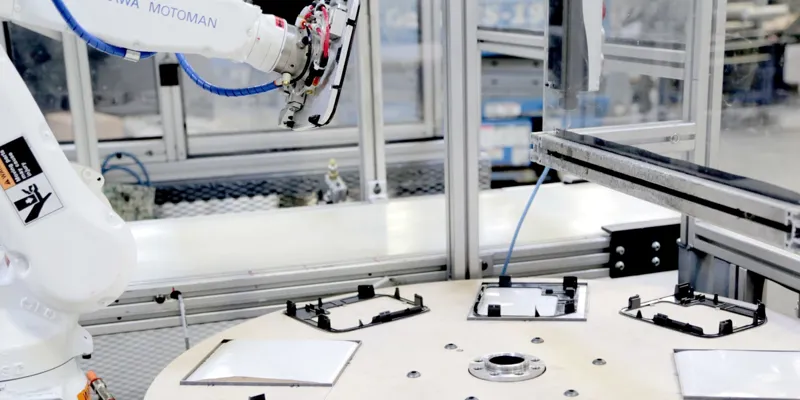
Value Analysis and Value Engineering VA/VE
Continuous improvement is not just a catchphrase at JBC – it’s a mission! And that mission does not end when parts leave our plant. We welcome the opportunity to tour our customers' facilities and see how our die-cut parts are integrated into their systems. This has led to countless improvement initiatives resulting in significant savings in both time and materials.
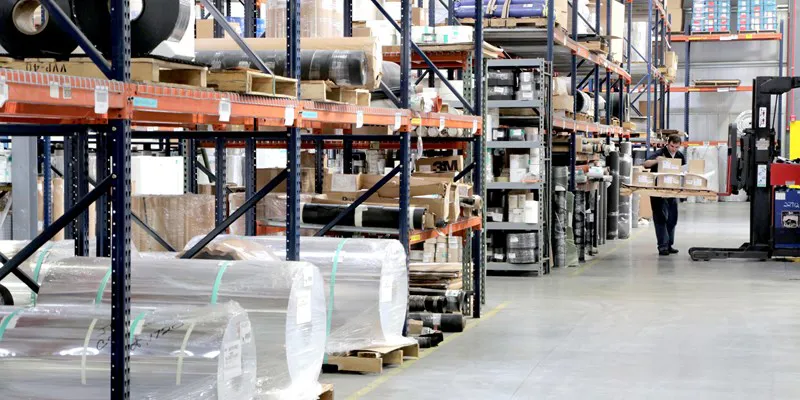
Supply Chain Solutions
The experts at JBC Technologies offer a number of services to help manufacturers reduce inventory, improve turn times, and streamline their supply chain. Options include custom packaging, kitting, retail packaging, custom labeling, consignment, and full Vendor Managed Inventory (VMI) programs.
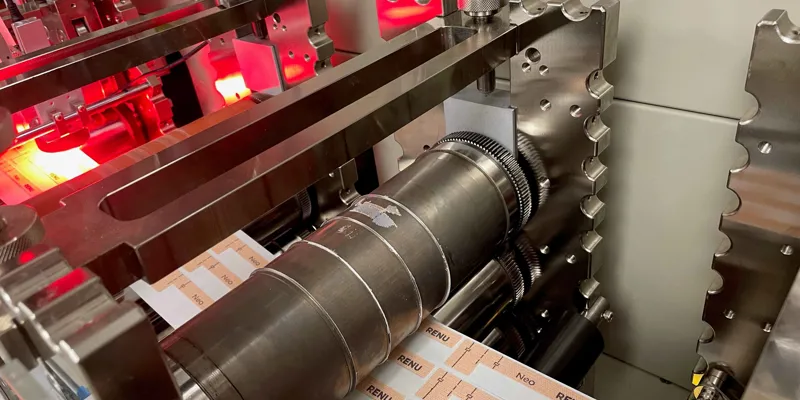
Digital Printing
JBC's inline digital printer enables us to print high-resolution full-color graphics on a broad range of flexible materials – from films and foams to bandage materials and non-wovens.
Expert Converting and Die-Cutting Capabilities
At JBC Technologies, we’re more than just a manufacturer of die-cut parts – we’re a collaborative partner that helps you determine the best, most cost-efficient solutions to your converting challenges.
Ready to work with a die-cutter that goes above and beyond at every stage of the game?
Our Conductive Tapes, Conductive Tapes, Heat Shielding Sheet, Die Cutting are featured on "Metoree", a product and manufacturer information comparison site for researchers and engineers.
The site provides useful information for engineers to compare and select products and manufacturers