5 Reasons for Adhesion and Cohesion Failure in Adhesive Tape
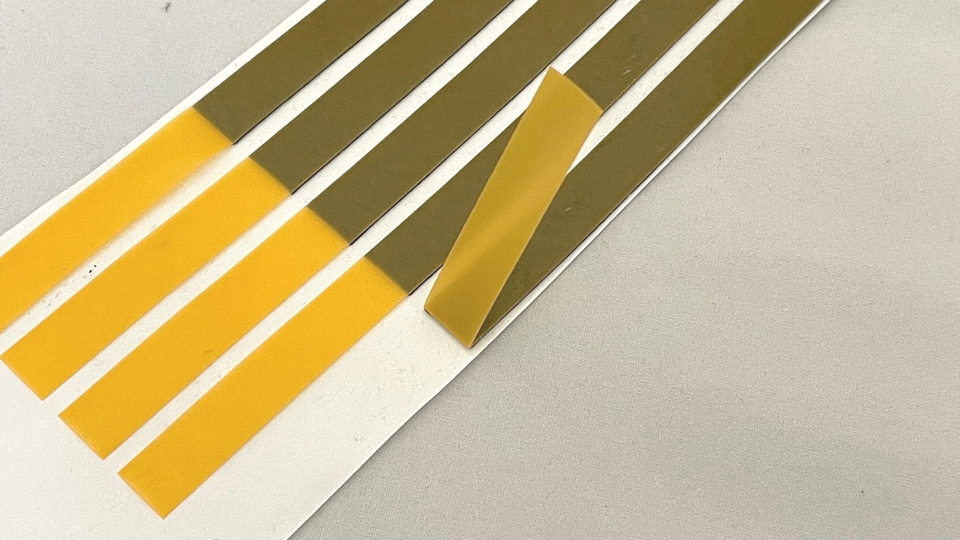
Your die-cut part is leaking, fell off, or it’s just not working. So what happened? One possible reason is the adhesive failed. This can happen for two core reasons: the adhesive failed at the bond line (adhesion failure) -- or it failed internally (cohesion failure).
Let's break that down...
What is Adhesion Failure?
Adhesion failure, otherwise known as de-bonding or failure, is one of the most common types of failure mechanisms. This failure mode occurs when the adhesive does not tear or split, but instead pulls away from one or both substrates. It can occur when two substrates are put under a load and prematurely separate and/or if the glue has not spread properly on the substrate. To make sure that the spreading of the glue (or other coating formulation) is sufficient, contact angle measurements can be used.
What is Cohesion Failure?
Cohesion failure, on the other hand, is when the failure or breakage that occurs within the adhesive material itself or inside the layer of a coating, rather than at the bond between the adhesive and the the surface to which the adhesive is applied. It happens because the adhesive material cannot withstand the applied stress or load and undergoes internal fracture or separation. As you might guess already, the cohesive failure will happen if the cohesive forces inside the adhesive are not strong enough. When cohesive failure is present, you will see a physical separation of the adhesive material.
Examples of adhesion failure and cohesion failure are pictured below.
Now that we know what adhesive failure is, here are 5 common reasons it happens:
1 - Inappropriate adhesive.
When choosing an adhesive, several factors must be taken into account. These include the substrates being joined, the environment it will be used in, and its expected operational duration.
2 - Environmental Factors.
The type of adhesive may be suitable for the application. However, unexpected changes in the environment can cause the adhesive to fail. Heat, cold, moisture, and the introduction of chemicals are all potential culprits.
3 - Surface Preparation.
Careful consideration must be given to the cleanliness of the two substrates. Grease, oil, dust, or dirt are a few examples that can cause poor bonding.
4 - Improper Curing of the Adhesive
Improper curing of the adhesive. Adhesives require specific actions in order to cure. Some of those include time, air flow, and the amount of pressure used during application. If any or all of these requirements aren’t followed, failure is possible.
5 - Lack of Elasticity and Strength.
Flexibility and adhesion levels are critical components to think about when selecting an adhesive. The specific type and amount of stress on the joint must be accounted for. Below are some examples of joint stress.
- Cleavage Stress: Cleavage is pull concentrated at one edge of the joint, exerting a prying force on the bond. While one end of the adhesive joint is experiencing concentrated stress on the leading edge, the other edge of the joint is theoretically under zero stress. Cleavage occurs with two rigid substrates.
- Shear Stress: Shear is pull directed across the adhesive, forcing the substrates to slide over one another. Here again, the force is in-plane, and the force is distributed across the entire area of the bond line.
- Tensile Stress: Tensile is pull exerted equally over the entire joint. Pull direction is straight, in-plane, and away from the adhesive bond. Force is distributed across the entire area of the bond line.
- Peel Stress: Peel is a pull that is also concentrated at one edge of the joint. One of the substrates is flexible, resulting in even more concentration at the leading edge than with a cleavage joint.
As you can see, there are many factors that lead to the success or failure of your application. If all of this seems too overwhelming to handle on your own, feel free to call us. We’d be happy to help.
A 3M Preferred Converter, JBC Technologies provides innovative die-cut solutions for leading manufacturers. These include adhesive-backed gaskets, seals, heat spreaders, fasteners, protective films, thermal and acoustic insulation, and more. Our customers benefit from our strong engineering focus and emphasis on providing value during the full product lifecycle.