Die-Cut Aerogel Alternatives for Mitigating Thermal Runaway in Battery Applications
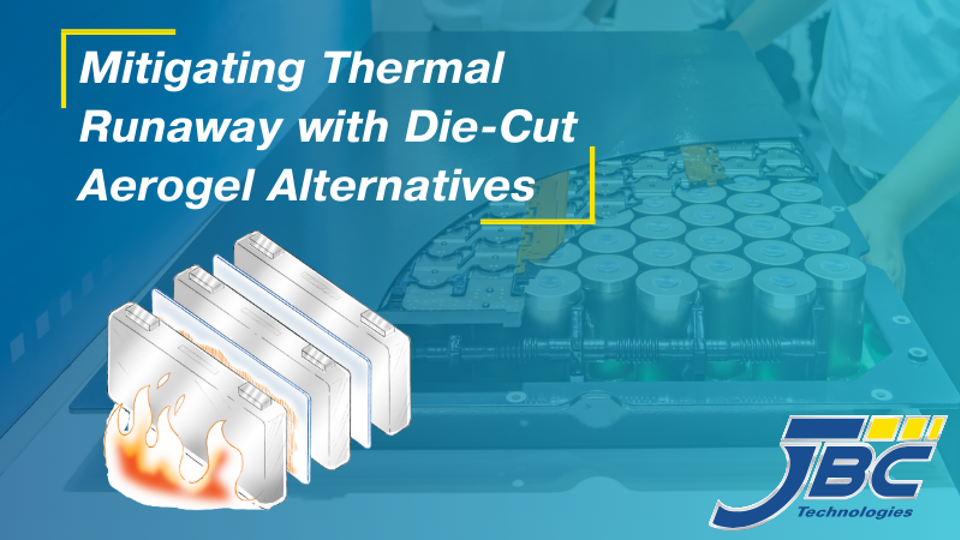
Materials science is always evolving...
When one material becomes the go-to choice for a certain application, it won't be long until an equally high-performance alternative turns up.
Because of their lightweight and thermally insulative properties, aerogels have become a popular solution for mitigating thermal runaway and lightweighting in battery applications.
Aerogels are:
|
![]() |
Yet for all these positives, a few drawbacks make it important to weigh some alternative options.
Not only do aerogels come with a high price tag, but they are also inherently dusty, require full encapsulation, and are difficult to convert from roll goods to finished parts. Due to the pillow-like nature of the material, aerogels are also prone to deformation or settling over time as they are exposed to the day-to-day cycling vibration inherent in the charge/discharge cycle of the battery. This, over time, can lead to uneven protection and distribution of coverage.
To avoid these challenges, engineers are turning to alternative flexible battery materials, die-cut to meet their exacting specifications. Today’s material spotlight features four high-performance thermal management materials that are often used for cell-to-cell cushioning and protection in battery applications.
Let’s take a closer look…
AIS ContraFlame® FCP Series
Newer to the market is AIS’s Contra Flame FCP Series – a family of cell-divider products for both pouch and prismatic cells that offer fire protection, compressibility, thermal insulation, and durability. At high temperatures, FCP material will create a highly stable ceramic barrier that is resistant to temperatures of up to 1300 °C, protecting the surrounding cells from thermal runaway propagation.
Key Performance Properties
|
||
Max Temperature |
1300°C |
1300°C |
Operating Temperatures |
-40 to 200°C |
-40 to 200°C |
Thickness |
2 to 10 mm |
2 to 10 mm |
Dielectric Strength |
10 Kv/mm |
10kv/mm |
Thermal Conductivity |
.127 w/mK |
.137 W/mk |
Density |
350 to 500 kg/m³ |
350 to 500 kg/m³ |
Pros:
-
Low Thermal Conductivity
-
Electrically Insulating
-
Lightweight Compression Characteristics
Cons:
-
Firmness: Off-the-shelf products are typically not rigid enough for pick and place automated assembly, although company representatives have highlighted that firmer solutions are currently under development.
Check out AIS in action:
View the material data sheets here:
Morgan Thermal EST™ Compression Papers
Morgan Thermal’s EST Compression Papers were designed specifically to accommodate the cyclical expansion and contraction that pouch and prismatic cells experience during the day-to-day operation of the battery as well as providing cell-to-cell thermal runaway protection.
Key Performance Properties
|
EST C30 |
EST 310 |
Max Temperature |
1300°C |
1300°C |
Operating Temperatures |
300°C for compression, 1000°C for continuous thermal |
300°C for compression, 1000°C for continuous thermal |
Thickness |
0.8 to 6mm |
0.8 to 6 mm |
Dielectric Strength |
2 kv/mm |
2.1 kv/mm |
Thermal Conductivity (20°C-1000°C) |
0.04 to 0.20 W/mk |
.04 to 0.16 W/mk |
Density |
240 to 310 kg/m³ |
400 to 510 kg/m³ |
Tensile Strength |
>205 kPa |
>1350 kPa |
Pros:
- High temperature resistance
- Compression properties
Cons:
- Encapsulation needs: Currently, EST papers require full encapsulation for dimensional stability and dust reduction, but the company is currently working on a no/low dust alternative.
Read our full EST Q&A with R&D Engineer, Jensen Plummer, here!
View the material data sheet: morgan-advanced-materials-_-est-compression-paper_eng.pdf
Rogers PORON EVExtend®
Rogers PORON EVExtend ® is a family of battery pad products that help combat cell pouch expansion and extend the battery life of prismatic, solid-state, and pouch cell batteries. EVExtend material simultaneously absorbs compression and vibration, which enhances pack durability and use-life while delaying further heat transfer in thermal runaway events.
Key Performance Properties
Poron EVExtend 43 | Poron EVExtend 71-20118 | Poron EVExtend 71-25118 | |
Max Temperature | 121°C | 121°C | 121°C |
Operating Temperatures | -20°C to 90°C | -40°C to 90°C | -40°C to 90°C |
Thickness | 1-3mm | 3.0mm | 3.0mm |
Dielectric Strength | 128 V/mil | 60 V/mil | 78 V/mil |
Thermal Conductivity | 0.44 W/mk | 0.075 W/mk | 0.079 W/mk |
Density | 112 - 320 kg/m³ | 320 kg/m³ | 400 kg/m³ |
Tensile Strength | 345 kPa | 1379 kPa | 1723 kPa |
Pros:
- Excellent compression and cushioning
- Enhances overall pack durability
- Low-outgassing
- Easily converted for small, closed spaces
Cons:
- Higher thermal conductivity
- Lower temperature resistance compared to other alternatives
- Cost
View the material data sheets here:
Saint-Gobain Norseal® F Series
Norseal® F Series Silicone Foams are flame-retardant, low compression set foams with excellent conformability and convertibility. F Series foams come in three levels of firmness (F-12 being the least dense and F-20 being the most dense), which cover a wide range of compression needs.
Key Performance Properties
Norseal f-12 | Norseal f-15 | Norseal f-20 | |
Max Temperature | 1150 °C | 1150 °C | 1150 °C |
Operating Temperatures | -51 to 204 °C | -51 to 204 °C | -51 to 204 °C |
Thickness | 0.063 to 1in. | 0.063 to 0.500in. | 0.031 to 0.50in. |
Dielectric Strength | N/A | 111 V/mil | 80 V/mil |
Thermal Conductivity | 0.42 W/mk | 0.05371 W/mk | 0.074 W/mk |
Density | 12 Ib/ft³ | 15 Ib/ft³ | 20 Ib/ft³ |
Tensile Strength | 25 PSI | 30 PSI | 30 PSI |
Pros:
- Wide range of firmness levels
- Able to handle wide range of temperature swings
- Great compression set
Cons:
- Denser than aerogels
View the material data sheets here:
- Norseal® Silicone Foam Rubber, F-12 Series (TDS) | Saint-Gobain
- Norseal® Foam, F-15 (TDS) | Saint-Gobain
- Norseal® Foam, F-20 (TDS) | Saint-Gobain
Converting Solutions with JBC Technologies
Selecting the perfect thermal management material for your battery project is only half of the battle. What matters is converting these materials into usable, high-performance parts. That’s where JBC Technologies comes in…
JBC Technologies is an ISO 9001:2015 Certified die-cutter and flexible materials converter with over 35 years of experience providing custom die-cut solutions to the battery storage industry. Whether it is battery cell cushioning and spacers, module and pack level electrical and thermal insulation, EMI/RFI shielding, thermal runaway prevention, or custom die-cut gasketing and sealing solutions, JBC technologies provides material selection and design for manufacturability considerations to take your project beyond the prototyping phase into full-scale automated production. Based on our foundational pillars of supply chain optimization, engineering innovation, and manufacturing excellence, JBC is the key to transforming raw materials to high-performance solutions.
Contact us today to get started on your next battery storage project.