Pressure Sensitive Adhesives vs Spray Coatings
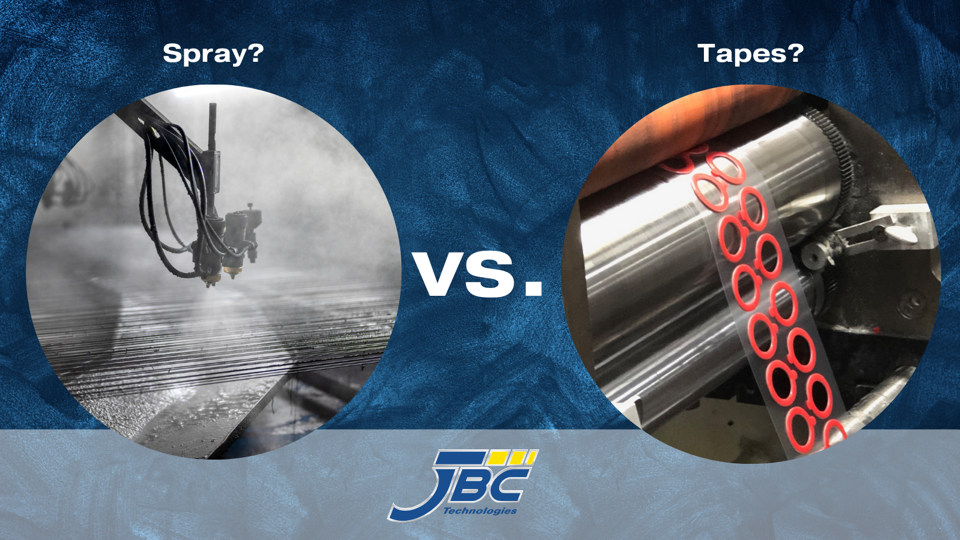
Benefits of PSAs in Battery Applications
With up to nine states already planning on phasing out gas-powered vehicles by the year 2035, the need for electric vehicles (EV), and by proxy, EV battery systems will only continue to grow in the coming years. So too will the need for EV battery manufacturers to find more efficient and cost-effective solutions to streamline the production process.
Pressure-sensitive adhesives (PSAs) with dielectric properties can offer many benefits with battery systems that traditional spray coating methods may lack. Although they both possess their own set of challenges, new advancements in dielectric tape technology such as the Avery Dennison Volt Tough™ Stretch, give manufacturers a level of flexibility and dependability that spray coating may not enjoy.
Today, we’re taking the time to highlight some benefits of dielectric PSAs and how they stack up against traditional spray coating applications. From weak spots to thermal management capabilities, learn about what sets custom die-cut specialty PSAs with dielectric properties apart from spray coatings.
Challenges of Spray Coating in Battery Applications
Spray coatings have been used for years for their dielectric properties and flexible applications. When compared to dielectric PSAs, spray coatings generally have a high structural bond. They are also relatively easy to apply using flexible automation. However, spray coatings come with their own set of challenges:
Inconsistent Thickness:
Due to the nature of spray coating application, it can be difficult to achieve a uniform level of thickness across a given area. This can lead to defects such as pinholing. Pinholes are defects on a spray-coated surface where electricity can arc through. They must be resprayed over to eliminate, adding another cycle to the production process. This can pose challenges to both manufacturing efficiency and product performance. For cooling components, a thinner more consistent coating is advantageous for increasing cell longevity and performance.
Curing:
Spray-coated items require an oven or UV cure station to properly cure. Not only does this process slow production throughput, but curing stations take up valuable floor space as well.
Weak Spots:
As previously mentioned, uniform thickness can be difficult to attain on spray-coated surfaces. This problem becomes especially apparent on sharp edges and tight corners where weak spots often occur. Spray-coating struggles to aptly cover these sharp corners leading to thin spots and un-optimized battery performance.
No Repositionability:
Unlike PSAs, spray coatings do not benefit from having any repositionability. Once the coating is applied, any adjustments that must be made must be addressed by re-spraying the problem areas. As we know, respraying creates consistency issues and costs precious production time and money.
Benefits of Custom Die-Cut Dielectric Tape
Custom die-cut pressure-sensitive adhesives have many applications in EV battery production such as chill plates, structure edge insulation, pack structure, cooling ribbons, and more.
PSAs with dielectric properties can offer solutions to some of the challenges associated with spray coating:
Uniform Thickness:
Cooling plates, cooling ribbons, and general cooling components are often made of aluminum, which is very electrically conductive. To prevent arcing, this aluminum must be separated from the battery by a dielectric barrier. Dielectric tapes serve as great dielectric barriers because they have a much more consistent thickness. In contrast to spray coatings, dielectric tapes have a thickness of around 50 microns with a low standard deviation, while spray coatings have a thickness of around 25 microns with a high standard deviation. The consistency supplied by tape is beneficial for proper heat flow from the cell into the cooling components, which promotes cell longevity.
Low storage risk/shop footprint:
Dielectric pressure-sensitive adhesive tapes are more storage-friendly than spray coatings. Not only are they safer to store, but they eliminate the need for cure stations altogether which allows for greater shop floor utilization.
Repositionability:
Because PSAs don’t fully set for 72 hours, any errors that must be addressed post-application can be fixed within this window of time. Unlike spray coatings which must cure and then be resprayed, PSAs can be readjusted as needed without having to worry about any of the challenges that respraying entails.
Customization:
With the help of a skilled converting partner like JBC Technologies, dielectric tapes can be custom die-cut to fit the exact specifications that your project requires, ensuring optimal fit and performance.
It is important to note that while dielectric tapes do come with a myriad of benefits, they aren’t without their own set of challenges. Surfaces with more complex geometry serve as a point of issue for PSAs. Dielectric tapes can sometimes struggle to create a high-quality bond on these complex, non-flat surfaces.
Summary
|
PSAs |
Spray Coatings |
Cure Speed |
Instant |
Needs UV oven/cure station |
Repositionability |
Able to reposition within 72-hour window |
None |
Thickness/Heat Flow |
Uniform thickness of 25 microns which is beneficial to heat flow |
Inconsistent thickness of 50 microns leading to unoptimized heat flow |
Shop Footprint |
Doesn’t require any cure stations |
Requires cure ovens/UV stations |
Weak Spots |
Struggles with complex geometry |
Struggles with sharp corners and edges |
JBC Technologies: Custom Die-Cut Solutions for You
With years of expertise and experience as a custom die-cutter and flexible materials converter, JBC Technologies is here to support your custom battery component needs. By taking rolls of high-quality performance materials and converting them to your exact specifications, JBC provides high quality custom parts with speed, precision, and consistency at extremely high volumes. We work hard to present your parts to you in a way that benefits your assembly and production throughput.
Tight tolerance die-cutting allows for the precise repeatability required for automated placement. Features like easy to remove extended liners, pull tabs, and adhesive zone coatings enable pick and place operations that can help speed up installation and increase assembly accuracy.
Our skilled team of engineers across 4 states utilize their years of experience as well as a wealth of industry connections to deliver high-quality solutions for a range of applications. From automotive, medical, electronic, HVAC and more, our vertically integrated production process ensures you complete your project efficiently and effectively.
Whether its custom die-cut PSAs, or a range of other die-cut EV battery solutions, let JBC convert your concepts into reality. Contact us today to get started on your next die-cutting project.