The Role of Electrical Insulation in High-Voltage Battery Energy Storage Systems
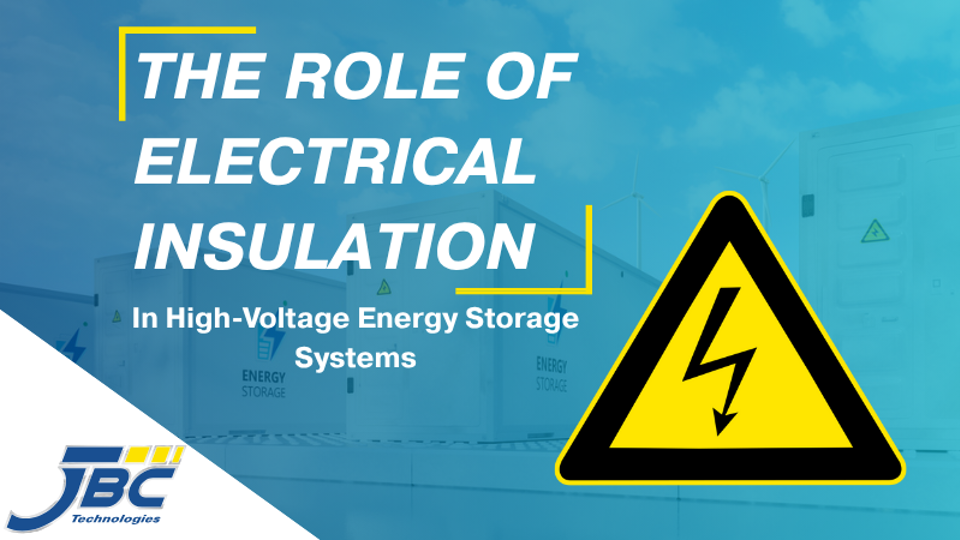
Safety and Performance Powered by Materials Converting
Battery power isn't going anywhere...
In 2024, the battery energy storage market was valued at 25.02 billion. Fast forward eight years, and the industry is projected to be worth 114.05 billion by 2032. With so much interest centering around energy storage systems, manufacturers will need to keep up with the speed of innovation.
Grid-level battery energy storage applications handle large amounts of electricity that entire communities and businesses rely on. With common voltages exceeding 1000V DC, these batteries and battery systems must be able to withstand high voltages for long durations without failure, making proper electrical insulation paramount for the functionality, safety, and longevity of these battery storage systems.
Today, we’re taking an in-depth look at the important role high-performance electrical insulation materials play in the day-to-day operations of BESS systems. From preventing electrical arcs and short circuits between densely packed cells to serving as thermal runaway barriers, we’ll cover how innovative flexible materials converting is key to robust electrical insulation solutions. For good measure, we also feature some common industry standards and test methods for insulation materials.
Addressing High-Voltage BESS Challenges with Die-Cut Electrical Insulation
So, what makes high-voltage battery energy storage system challenges unique?
High Energy Density The demand for greater energy output often leads to densely packed battery modules. Tight cell/module packing increases the risk of insulation breakdown via heat, pressure, or vibration. |
|
Voltage Stacking Generating such large amounts of energy involves thousands of individual cells connected in series, called “voltage stacking”. Series-connected cells or modules require precise insulation between high-voltage cells to prevent current bypasses and other cross-mode failures. |
|
Modular Assembly Many BESS designs need to be removable and reworkable for transportation, installation, and routine maintenance, making it critical that the electrical insulation solutions are precise and form-fitted, so that they can be reliably placed during assembly and reworkings without sacrificing insulating performance. Precision, tight-tolerance die-cut insulation components are critical for solving this. |
The Role of Die-Cut Electrical Insulation
Electrical insulation systems must be able to withstand the electrical distresses that come with typical and transient operating conditions in energy storage system operations, like switching surges, inrush currents, voltage sags, ground faults, and electrostatic discharge.
Preventing Short Circuits
How? Electrical Insulation maintains the physical and electrical separation between conductive components, including individual cells, cell groups, busbars, and enclosures. This prevents unintended current paths that could lead to localized heating, fire, or complete system shutdown. But the real challenge is achieving this insulation reliably, repeatably, and without sacrificing critical space or manufacturability. Materials like thin, high-dielectric PET films, 3M FRB, and Nomex® can be custom-cut to maintain proper electrical isolation in a lightweight, sleek package.
What does this look like?
- Thin die-cut films like PET with a laminated adhesive backing between cells
- Die-cut multi-functional spacers made of 3M FRB between battery module frames and pack housing that provide critical thermal and electrical insulation, as well as essential flame barrier protection
- Die-cut laminated polyimide film barriers around BMS circuitry and control boards to prevent unintended contact
PReventing Electrical Arcing
How? Die-cut electrical insulation can be used to ensure that voltage differences don’t result in the ionization of air or surrounding gases that could create conductive plasma paths. These paths can lead to dangerous electrical arcing, system damage, and even fires. For high-risk areas like busbars, terminals, and cell edges, precise, even coverage is imperative. Through custom die-cutting, flame and arc resistant materials like AIS Contraflame®, can be custom-cut to fit over the irregular geometries of weak spots like sharp edges and tight compartments, providing consistent, even coverage.
What does this look like?
- Managing creepage and clearance - As outlined in standards like IEC 62619 & UL 1973, creepage and clearance are important for preventing surface tracking and arcing in humid or polluted environments. JBC provides custom die-cut components that optimize these critical distances.
- Using arc-resistant materials like Nomex® and AIS Contraflame® between cells to mitigate the heat and electrical energy of an arc without breaking down
- Adding dielectric barriers at known high-voltage junctions like terminals and busbar crossings- Look to the Avery Dennison Volt Tough and Flame Tough Series of Tapes for high-dielectric and fire-resistant adhesion in these areas.
Thermal Management
How? A secondary, yet equally crucial role of electrical insulation is thermal management. High-voltage operating environments and many electrical failures, like short circuits and arcs, generate very high temperatures that can lead to thermal runaway events. Electrical insulation solutions need to be able to withstand these demanding high-temperature environments without fail. At JBC, we leverage material expertise and supplier relationships to help identify and convert thermal management materials into custom components that solve critical challenges for our end users. Working with a converting partner is the key to seamlessly integrating these thermal management materials into your battery system.
What does this look like?
- Selecting materials that meet UL 94 standards that are rated for long-duration exposure to heat, like specialized ceramics, mica, and aramid papers-This is critical for identifying materials that won’t lose their dielectric properties after sustained exposure to heat.
- Determining whether your insulation material needs to dissipate heat or contain heat- If dissipation is your goal, it’s important to select a material with good thermal conductivity, like graphite. When you’re looking to contain heat, look for materials with low thermal conductivity like silicone foams or aerogels.
- Identifying materials that minimize off-gassing when exposed to heat-Leverage your converting partners material selection expertise to select a material that won’t release harmful chemicals upon heat exposure.
Key Standards for Electrical Insulation
IEC Standards |
UL Standards |
IEC 60695
IEC 60695 is a series of standards that assess the fire hazard presented by various electrotechnical products.
|
UL 94
UL94 is a critical standard that measures the flammability of plastic materials when exposed to a flame. It’s important to look for materials that are UL 94 rated when selecting the right electrical insulation material to aid in dangerous thermal events.
|
IEC 62933
This is a comprehensive international series of standards dedicated specifically to battery energy storage projects. IEC 62933-2-1 is a specific portion of these standards that covers system-level safety aspects like fire hazards, electrical shock, and chemical concerns that are all addressed with proper electrical insulation.
|
UL 1973
This standard outlines necessary safety specs that insulation materials used within battery modules must comply with, including dielectric strength, insulation resistance, and fire resistance.
|
IEC 62619
IEC 62619 is an important international standard for the safety of lithium-ion cells and batteries in BESS applications, focusing on cell-level safety including thermal runaway, arcing, short-circuits, and fires.
|
UL 9540
UL 9540 is one of the most comprehensive BESS standards, outlining the requirements for electrical isolation, fire protection, and system integrity, helping inform the electrical insulation material selection process.
|
For a more in-depth look at UL Certifications, check out our whitepaper, UL Certification Demystified: Your Guide to UL Certification and Custom Die-Cut Components.
Common Test Methods for Electrical Insulation
Dielectric Strength Testing
This test is a primary indicator of insulating capability, helping determine the maximum voltage an insulating material can withstand before electrical breakdown occurs. This test is critical to selecting short-circuit and arc-resistant materials.
Thermal Cycling and Aging
This test measures a material's ability to withstand repeated temperature fluctuations for extended periods without losing its performance properties, simulating real-world operational stress. Understanding how a material handles dynamic battery environments under long-term stress is critical for battery longevity.
Volume and Surface Resistivity
This test is important for measuring the resistance of a material to current flow across its surface. High resistivity prevents leakage currents and keeps the insulation strong.
Flammability and Fire Resistance Testing This test measures how well a material handles intense thermal environments, including its ability to prevent thermal runaway propagation and self-extinguish. Check out AIS Contraflame® taking on this thermal runaway test: |
|
A Trusted Partner for High-Voltage Solutions
For grid-level energy storage applications that millions rely on for day-to-day power, compromising safety or performance simply isn’t an option. In such high-stakes applications, you need precision components that won’t fold under the pressure. That’s where JBC comes in…
JBC Technologies is an ISO 9001-certified die-cutter and flexible materials converter with over 35 years of experience providing engineered die-cut solutions. From grid-level commercial and industrial energy storage to EV batteries and renewable energy solutions, JBC leverages years of process engineering expertise and relationships with industry-leading material suppliers to help solve a wide range of BESS/EV challenges, including thermal and electrical insulation, EMI/RFI shielding, attachment tapes, gaskets, vibration dampeners, and more.
Our partnership goes beyond supplying die-cut components. JBC's dedicated in-house engineering team collaborates directly with your R&D and design teams from the earliest stages, providing crucial Design for Manufacturability (DFM) insights that optimize your designs for precision, reliability, and efficient mass production.
This strategic partnership ensures that your vision translates flawlessly from concept to scalable reality, reducing technical risks, accelerating your NPI timelines, and securing a consistent, high-quality supply chain for your most critical die-cut parts.