Die-Cut Adhesives – Applications and Benefits Within the Electric Vehicle Battery Pack
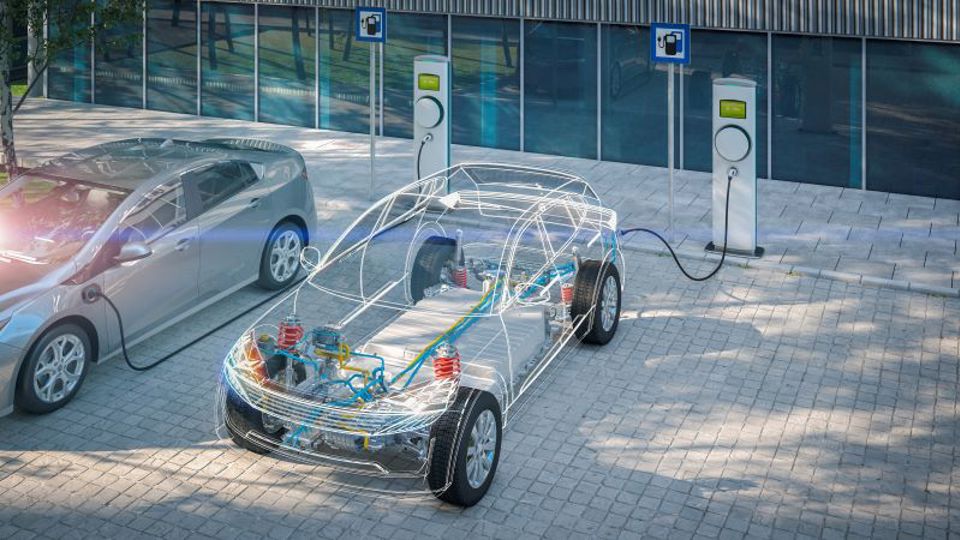
When you read the words “electric vehicle” chances are one of the first things to come to mind is the battery. What might not be so readily apparent is the hidden complexity of these mobile power sources. Here’s an image for you — Matryoshka dolls. You know the ones, smaller dolls inside larger dolls, inside larger dolls...et cetera. The largest “doll” of the typical EV battery is the main pack. Inside the main pack are several modules, each of which is composed of numerous smaller cells. What’s more, there are countless smaller parts and materials bonding, sealing, insulating, gasketing, and protecting all these battery components.
Within the sealed-off world of the EV battery, there exist many applications for custom die-cut materials, in particular, tapes and adhesives. What lies ahead will be an educational and entertaining romp through the many benefits one might see when choosing to use die-cut pressure-sensitive adhesives and tapes instead of mechanical fasteners and liquid adhesives and sealants. Our sincere hope is that by the time you’re done reading this, you’ll no longer look at EV batteries in the same way again and, if we’ve done our job, this new perspective will include custom die-cut parts from JBC Technologies.
Bonding and Sealing
In any list of adhesive benefits, the first place to start is bonding. After all, that’s what adhesives do best. A few examples of where die-cut adhesives can be used for bonding and sealing within the battery pack are:
- Cell-to-cell bonding — Die-cut double-coated tapes are ideal for joining one cell to another to contribute to the overall structural integrity of the battery pack.
- Compression pads — Die-cut tapes and adhesives can also be used to bond the compression pad foam that is inserted in between battery cells to protect the cells from damage.
- Pack seals and gaskets — As a final point, adhesive can be used to secure high-temperature foams designed to seal out contaminants, dampen sound, and reduce friction between components in different areas in and around the battery pack. In some ways, this application is no different than sealing any other pack or gasket. In others, it is much different. The difference lies in the performance properties required of the adhesive.
But why use die-cut pressure-sensitive adhesives over liquid adhesives? Pressure-sensitive tapes have advantages over their liquid counterparts in that they can be laminated directly to the foam and die-cut into your specific size and shape requirements. In addition, they require no cure time, provide immediate strength, and provide full coverage adhesion. Due to challenges with surface energy, there is also a distinct advantage to using a differentially coated tape, when joining dissimilar materials. Lastly, die-cut adhesives allow for a thin, consistent profile, a continuous bond area, and instant bonding.
For more information, visit: tapes.averydennison.com/evbattery
Protecting High-Performance Materials
In addition to bonding compression pads between battery cells, or securing pack seals and gaskets, and performing other basic “fastening” functions, both single-coated and double-coated tapes can be used to encapsulate the performance materials that do the heavy lifting to reduce thermal propagation between cells. Ceramic papers and blankets, for example, offer thermal runaway mitigation properties but tend to be flakey or dusty. A high-temperature rated adhesive with a filmic carrier such as FT 8065 from Avery Dennison Performance Tapes can be used to envelop the material and seal out flakes and dust from the sensitive battery components.
Reducing Thermal Runaway
As engineers continue to innovate to extend the driving range and increase charging speed, they are also working to improve the overall safety and performance of the vehicle. Li-ion batteries produce significant heat when in use and during charging, making thermal management critical to protecting both the battery and the driver. In the event that one battery cell malfunctions, the heat needs to be contained so as not to move from one cell to the next. While a tape or adhesive alone will not stop a thermal runaway event within the battery pack, it can play an important part in the success of the overall material stackup that does. If you choose a tape that is not flame retardant, electrically insulated, or formulated to form a strong bond with the substrate you are bonding to, the adhesive could degrade and fall off, you could see arcing or shorting in the battery pack. Or, if the adhesive is not flame retardant, it could even contribute towards the creation of a fire.
Thermal Interface Management
Thermal interface materials (TIMs) are an important part of many EV battery designs. They perform the critical function of transferring heat away from heat-generating components to prevent overheating, improve reliability, and extend the life of the mission-critical electrical elements of the vehicle, including but not limited to, elements within the battery pack. They are often used between the cells of a battery module or on the bottom plate of the battery. Because they are used in close contact with electrical components, high dielectric strength is a must — both in the TIM itself, and the adhesive used to bond it.
Adding Dielectric Strength
Dielectric Strength is defined as the maximum electric field that a material can withstand without experiencing failure of its insulating properties. The higher the dielectric strength, the better a material can prevent electrical conductivity. By laminating a filmic tape that offers high dielectric strength to your thermal management material, you can improve the performance of the overall composite, protect against galvanic corrosion, and reduce the shorting or arcing that could occur if the material is not properly electrically insulated.
Enabling Multi-Functional Material Stackups
In many cases, the answer to identifying the ideal material to solve a particular EV battery challenge lies with not one, but two or three materials married together to form one composite construction that is greater than the sum of its parts — a stackup. Unlike liquid adhesives, tape products can be laminated to other performance materials like ceramic papers, polyurethane foams, and dielectric films, and then die-cut to the specific size and shape required. These multi-layer composites provide flame retardancy, thermal conductivity, dielectric strength, and can even help reduce buzz, squeak, and rattle. In addition to bonding and increasing dielectric strength, the adhesives can absorb vibration between materials and reduce squeaks and noises in the pack.
Consider these hypothetical situations:
- flexible graphite plus foam;
- flexible graphite plus ceramic paper plus foam;
- mica plus polyurethane foam plus ceramic paper plus peel-and-stick adhesive with a dielectric film carrier
You get the picture. None of these constructions would be possible without the adhesive to bond the layers together and a flexible materials converter like JBC Technologies with the acumen to turn concepts into reality.
Converters can add even more benefit by adding pull tabs, extended liners, and other value-add solutions that can be assimilated into an automated production line to speed production at your plant.
Turn to JBC Technologies for EV Battery Material Converting Needs
For all these benefits, choosing the right adhesive for an application is never easy. It’s even less so when it is to be used in an application as critical as the battery pack of an electric vehicle. You need to consider the flammability piece, the insulation piece, and even the processing piece. You’ll also want to consider how the die-cut parts will be included in the overall assembly. Will the assembly be automated? Do you need a light release liner? Will a slight modification to your part design reduce costs while adding benefit? Or improve the manufacturability of the part? That’s where the experts at JBC come in. We’ll not only work with our many material providers to help you pick the right adhesive, the right liner, and the right carrier stock for your application, we’ll also engage our seasoned processing and manufacturing engineers to make sure the part provides the best total value to you and your end customer.
For over three decades, we’ve been putting our engineering and manufacturing expertise to work transforming rolls of foam, insulation, adhesive tape, plastic film, melt-blown fabric, and even metal foil, into custom die-cut parts that have helped thousands of manufacturers solve critical design challenges. Interested in learning more? Give us a call at 440-327-4522 or fill out this simple form and we’ll be in touch soon. Let us help turn your challenges into solutions.