
DIE-CUT PARTS FOR ENERGY STORAGE APPLICATIONS
Whether you need to prevent electrical shorts or arcs, protect against thermal runaway propagation, dissipate heat, isolate heat, or insulate battery cells, JBC has the engineered die-cut solution for any battery storage application.
With over 35 years of experience converting high-performance foams, foils, tapes, ceramics, and other flexible materials into functional components, JBC Technologies' dedicated in-house engineering team collaborates directly with your R&D and design teams from the earliest stages, providing crucial Design for Manufacturability (DFM) insights that optimize your designs for precision, reliability, and efficient mass production.
This strategic partnership ensures that your vision translates flawlessly from concept to scalable reality, reducing technical risks, accelerating your NPI timelines, and securing a consistent, high-quality supply chain for your most critical die-cut parts.
Let us help you find solutions to:
PRevent short circuits and electrical arcing
boost overall pack integrity
Insulate and isolate battery cells
Improve battery longevity
mitigatE thermal Runaway
And much more
How Die-Cut Components Improve the Safety and Efficiency of Grid Storage Batteries

Tight cell clusters, extreme temperatures, high voltages, and irregular shapes: these are the average operating conditions that die-cut ESS components must brave, day in and day out. Custom die-cut components are critical for meeting the challenges of the battery energy storage industry, including electrical and thermal insulation, pack gasketing/sealing, cell-to-cell propagation protection, and mechanical absorption.
Through tight-tolerance die-cutting, a stringent quality management and defect detection system, value-added services, and a dedication to engineering custom solutions, JBC provides custom ESS components that can be seamlessly integrated into your battery system. Custom die-cut components are ideal for modular battery assemblies and can be scaled along with your production needs, from small volume prototyping to high-volume automation.
Optimizing Your Die-Cut ESS Component Design for Manufacturability and Scalability
JBC's dedication to engineering innovation powers our passion for providing design for manufacturability (DFMA) considerations and optimizing the design of your ESS components. Through value-added services, scalable production support, and diverse converting capabilities, JBC's engineers work as an extension of your engineering team to add value wherever possible. |
Look to JBC Technologies for...

Electrical Insulation
Custom die-cut electrical insulation components are key for preventing dangerous electrical arcs and short circuits in dense battery packs, while supporting overall pack integrity, longevity, and performance. Die-cut flexible materials like polyimide films, PET, and aramid papers can be custom-cut to very tight tolerances to provide equal coverage in cramped compartments or weak spots like busbars and connectors.

Thermal Management
Die-cut thermal management components improve battery performance and safety by allowing for higher charging rates without damaging the battery and isolating heat flow between both the cell and pack levels. A converting partner like JBC Technologies transforms graphite, ceramic fibers, silica-based mats, polyurethanes, silicone foams, and other flexible materials into functional, scalable thermal management solutions.
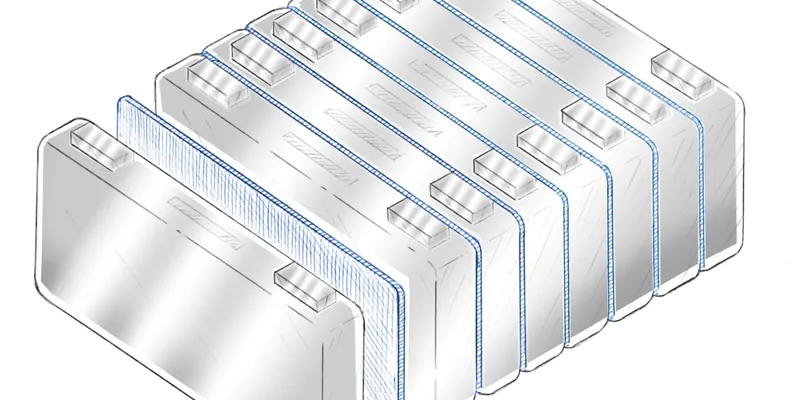
Battery Cell Separators and Compression Pads
Battery cell battery separators and compression pads maintain a fixed, precise gap between battery cells and modules to prevent direct contact with the anode and cathode, short circuits, thermal events, and mechanical damage. JBC converts everything from silicone elastomers, aerogels, EST papers, polyimide films, rigid plastics, and more into custom functional battery divider solutions.

Gaskets and Seals
Utilized on a cell, pack, and module level, custom die-cut gaskets and seals protect sensitive battery components from moisture, dust, and other contaminants, preventing the leakage of electrolytes and gases. JBC converts silicone, fluoroelastomer, microcellular polyurethane, closed-cell EPDM, and many more flexible materials into custom battery gaskets and seals.

With a U.S.-based supply chain, JBC helps mitigate the uncertainty of global supply chains for consistently sourcing battery solutions.
Learn more about the benefits of a U.S.-based converting partner here!
High Speed Die-Cutting Services for Large-Scale Battery Production
As a vertically integrated material solutions provider, JBC Technologies has a diverse range of die-cutting and flexible materials converting capabilities. From complex multi-layer laminating to simple roll slitting and butt-cutting, leveraging this wide range of converting capabilities is the key to finding the perfect custom solution for your battery energy storage project.
JBC's converting capabilities include:
-
Wide web platen die-cutting
-
Laser cutting
-
Hot/cold roll laminating
-
Slitting
-
Sheeting
-
Inline Printing
-
Embossing
JBC provides custom battery storage solutions for:

Long Duration Storage
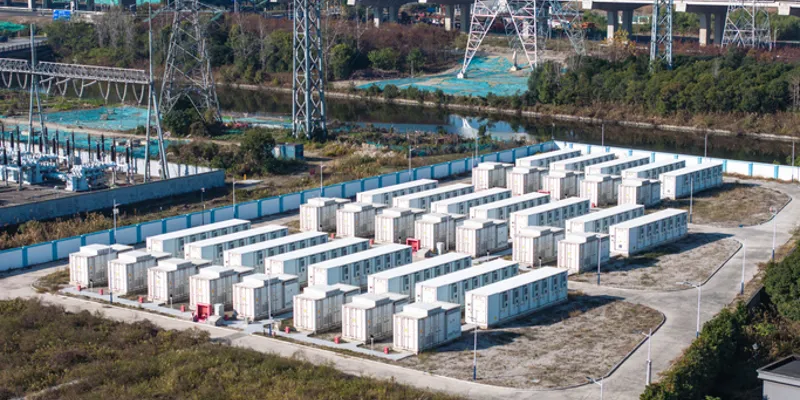
Grid Storage

Commercial and Industrial Energy Storage

Residential Energy Storage
Additional Resources: Energy Storage Industry
Get Started Today Submit Your Project
With electrification on the rise, you need a battery converting partner that's able to move at the rapid speed of innovation. With over 35 years of experience finding engineered solutions to various battery challenges, JBC Technologies is a partner you can trust for custom battery components. Providing full product lifecycle support from rapid prototyping to high-volume production, JBC applies expert materials and processing expertise to solve a wide range of battery storage challenges.
Ready to work with an experienced die cutter that focuses on the total solution?