5 Things to Consider When Choosing Material for Your Seal or Gasket
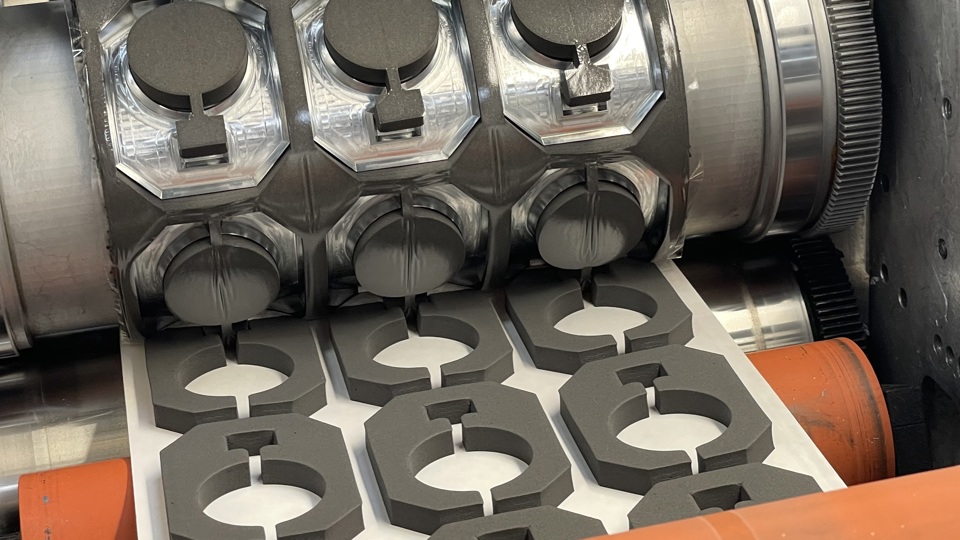
The importance of selecting the right material for your die-cut seal or gasket cannot be overstated. The wrong material can cause a seal or gasket to fail resulting in equipment damage, production delays, shorter product life, or even injury. Material selection should always begin with an assessment of the application in which the die-cut seal or gasket will be utilized to ensure it meets your specific needs. However, several common factors such as temperature, environment, industry standards, compression set, and durometer should be considered.
Let’s take a closer look at each of these five things:
1. Temperature
The first consideration when selecting a material for your seal or gasket is temperature since it can change the characteristics of the material. Extreme heat, cold, or widely fluctuating temperatures can affect material sealing properties, maximum allowable stress, and overall performance. Typically, as application temperatures rise, material options become more limited. In addition, the amount of time a material is exposed to the maximum temperature will guide your material selection.
Check out our blog 8 Gasket Materials for Mid-Range Ambient Temperature Applications for a few suggestions.
2. Environment
Several environmental factors can impact the longevity of a gasket. In addition to temperature as described above, these four factors are vital to the success or failure of your seal or gasket:
- UV Exposure: Exposure to UV light can result in seal or gasket degradation.
- Moisture Resistance: Absorbent materials can deteriorate when exposed to moisture leading to gasket failure.
- Chemical Resistance: Acidic, corrosive, toxic, or abrasive chemicals will impact on the integrity of the seal or gasket.
- BSR & NVH Reduction: Vibration can damage sensitive components, leading to product failure and distracting noises.
For examples of material well-suited to meet these environmental requirements, check out our blog Preventing Gasket Failure Part 3: Environment.
3. Product/Industry Standards
Standards for seals or gaskets vary depending on your product, industry, and location. Industries such as Automotive, Food Services, Pharmaceutical and many more have specific material requirements that must be met. It is important to work with a manufacturer that can ensure you meet the proper certifications.
Additionally, here are a few broad certifications that may be applicable:
- ASTM – American Society for Testing and Materials
- UL – International Safety
- MIL-SPEC – Military
- AMS – Aerospace Material Spec
- FDA – Food and Drug Administration
- ANSI – American National Standards Institute
- NSF – National Sanitary Foundation
4. Compression Set
A material’s compression set is the amount of permanent deformation that a seal or gasket sustains when put under pressure or force. Seal or gasket performance is diminished over time and repeated compression reducing seal effectiveness due to gaps, leaks, or application failures. It is important to note that material recovery abilities matter more with periodic vs constant compression. Standards for measuring compression set vary; therefore, you should work with a trusted partner to help you select the best material for your application and perform real-world testing to determine the suitability for your intended use.
For more detailed information on compression set and how it impacts seal and gasket performance, check out Preventing Gasket Failure Part 1: Compression Set.
5. Durometer
Durometer is a standardized way to measure a material’s hardness or, for a foam, its firmness. Durometer testers have measurement scales that range from 0-100 indicating the amount of force needed to achieve a certain level of indentation. Lower numbers indicate soft, flexible materials while higher numbers indicate harder materials. Variations in material hardness require testers with different probe shapes and spring loads to create the specific amount of indentation. Testers are selected by material classification as listed below.
- Shore 00 – Extremely soft materials like foam and cellular sponge
- Shore A – Solid rubber materials used for O-rings and rubber sheeting
- Shore D – Hard plastics and very hard rubber compounds
Durometer is a key factor in sealing performance. Seal or gasket material must be soft enough to fill the gap between two surfaces without extruding from the joint, yet hard enough to withstand the pressure or impact it will encounter. Selecting material hardness for your application can be challenging. It is advisable to work with an experienced manufacturer to identify the best, and most cost-effective material for your application.
Interested in more information on durometer and its effect on sealability? Check out Preventing Gasket Failure Part 2: Durometer.
Selecting the Right Converter is Key
At JBC, our years of flexible materials converting experience and vast supplier network can help you find the right balance between performance quality and cost to meet your project needs. We encourage our customers to prioritize performance quality when selecting a material for seals and gaskets whenever possible. Improper material selection can be very costly down the road if seals or gaskets fail and result in product or equipment failure or compromised safety. Consulting with one of our technical experts early in your product design phase can help ensure the success of your next project. Contact our team today.