Achieving Aerospace-Grade Precision: 5 Tips for Tight Tolerance Die-Cutting You Need to Know
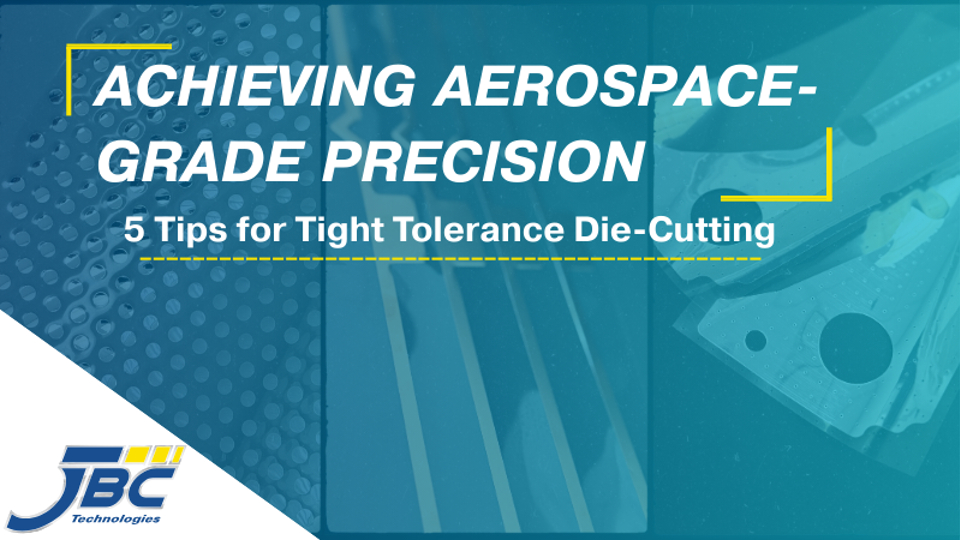
“Aerospace-grade precision” isn’t just a buzzword…
From challenging operating environments to expensive payloads and demanding performance requirements, die-cut aerospace components must perform in conditions far beyond typical industrial applications. The functionality of components like multi-layer thermal insulation or irregularly shaped EMI/RFI shielding often hinges on their dimensional soundness. Slight variations, no matter how small, may lead to uneven coverage of mission-critical components, introducing safety risks, costly redesigns, and even dangerous product failures.
However, this need for precision must be balanced with the inherent limitations of flexible materials and the constraints of the die-cutting process. Factors like material thickness, density, elasticity, and rigidity can significantly impact a converter's ability to hold tight tolerances.
To help you navigate your next tight tolerance aerospace project, we’ve put together these five helpful material tolerance tips to get you started on the right track:
- Prioritize Function Over "Off the Shelf" Default Tolerances
- Account for Material Density
- Design with Purposeful Material Thicknesses
- Consider Strategic Lamination for Rigid Materials
- Add Carriers to Improve Dimensional Stability of Elastic Materials
Machined Tolerances vs. Material Tolerances
But before we get into our tips, it’s vital to understand a key difference: the difference between machined tolerances and flexible material tolerances.
- Machined tolerance refers to the "on-paper" tolerance that a die-cutting machine is capable of holding. These tolerances reflect the mechanical accuracy and capabilities of the machine.
- Flexible materials tolerance introduces another level of complexity. They refer to the behavior that certain materials exhibit when under pressure based on their thickness, elasticity, density, and rigidity. Here, the challenge isn't just the machine's capabilities, but rather the limitations of the specific material itself. These factors can make it more challenging to hold tight tolerances — especially as a material gets thicker, denser, and more rigid. This means that although a machine can hold a certain tolerance on paper, the actual capabilities are influenced by each material's dynamic properties.
Now, let's look at some helpful material tips for tight tolerance converting...
5 Tight Tolerance Tips: The Key to Launch Readiness and Reliable Performance
1. Prioritize Function Over "off the Shelf" Default tolerancesIt’s common for some engineers to revert to common “default” tolerances that, while standard, may be overly restrictive and unnecessarily drive up costs without adding functional value. Work with your converting partner to determine whether your tolerance is truly critical to the functionality of the part. This will help you optimize costs without sacrificing quality. |
|
2. Account for Material DensityMaterial density essentially refers to the mass per unit volume of a material, or in other words, how much “stuff” is packed into a given space. Denser materials typically require more force, slower cuts, and alternative blade angles to ensure a smooth, defect-free cut. Less dense materials, like low-density foams and rubbers, are more prone to compression and deflection while cutting, which can lead to uneven edges. When selecting materials, understand that the density of your desired material will have a direct effect on the tolerances you will be able to hold. |
|
3. Design with Purposeful Material ThicknessesMaterials often come in certain standard thicknesses, but it’s important to determine the exact thickness that’s truly critical for your parts’ performance. Material thickness affects the feasibility of certain die-cutting techniques, the type of tooling needed, and the risk of defects. The thicker a material becomes, the more difficult it is to hold tight tolerances, and the more susceptible it becomes to defects like apple coring. Ensure your material thickness is purposeful; only go with the thickness that is necessary for functionality in order to consistently hold tighter tolerances. |
|
4. Consider Strategic Lamination for Rigid materialsHighly rigid materials may crack or fracture under pressure, creating dimensional defects and inconsistencies. In place of highly rigid materials, laminating a thin layer of your high-performance, rigid material to a less rigid, more compliant backing can help achieve the same performance properties without affecting tolerance or performance. |
|
5. Add Carriers to Improve Dimensional Stability of Elastic MaterialsElastic materials, like some pressure-sensitive adhesives, can snap back or deform after being cut, distorting the dimensions of the final part. Elasticity makes it difficult to maintain consistent part dimensions and often requires wider tolerances. To add stability to elastic pressure-sensitive adhesives, talk with your converting partner about adding a stable carrier to increase dimensional stability. |
Our Precision Toolkit: Precision Die-Cutting Technologies for Tight-Tolerances
Now that you know what factors affect a converter's tolerance capabilities, it's important to understand the capabilities themselves. These are the technologies that make up JBC's tight tolerance toolkit:
For High Volume, Intricate Components
For high-volume runs of intricate components, rotary die-cutting capabilities enable high-speed production of thousands of components without sacrificing tolerances or quality. For parts that have made it through design validation, rotary die-cutting helps you take your product to market quickly. Think scalable, high-volume efficiency with uncompromising precision. |
![]() |
![]() |
For Thick, Multi-Layered Materials
For thicker components like multi-layered thermal insulation, flatbed die-cutting delivers powerful cuts to a wide range of thicker, denser materials. Though not quite as precise as rotary or digital cutting, flatbed die-cutting excels for thick materials and medium production volumes.
|
For LOW-VOLUME Prototyping
Perfect for low-volume prototyping and the design validation phase, digital die-cutting delivers highly precise components with no tooling investment. Digital die-cutting is an important tool for accelerating NPI initiatives, allowing you to quickly test multiple designs and materials with little investment.
|
![]() |
![]() |
For Traceable Quality Management
JBC utilizes a multi-camera inline vision system to detect even the smallest dimensional anomalies in die-cut components. Using a three-tiered “good, better, best” system, this quality management system tracks and logs each part’s exact dimensions in real time, allowing for instant defect detection and part traceability. This tool is critical for guaranteeing that every part that leaves the production line meets your exact tolerance needs.
For a more comprehensive look at our inline vision system, check out this blog! |
Partnering for Performance: The Value of an Aerospace Converting Partner
Custom die-cutting technologies provide scalable precision, enabling the production of thousands of dimensionally identical components. This precision guarantees your components fit right the first time for faster product integration/NPI launch, increased safety/performance, and cost efficiency. The result? Die-cut thermal and electrical insulation, brightness mitigation, EMI/RFI shielding, and vibration-damping solutions that let you go to market faster and with greater confidence.
For aerospace components where quality is non-negotiable, you need a manufacturing partner as dedicated to the total solution as you are…
JBC Technologies is an ISO 9001:2015 Certified die-cutter and flexible materials converter with over 35 years of experience providing engineered solutions to the aerospace, EV battery and energy storage, medical, automotive, and industrial markets. Founded on the foundational pillars of supply chain optimization, engineering innovation, and manufacturing excellence, JBC provides full product life-cycle support, from small volume prototyping to high-volume manufacturing. With a team of degreed engineers and relationships with industry-leading suppliers, JBC leverages materials and process engineering expertise to transform a wide range of flexible materials like foils, foams, plastics, and more into functional die-cut solutions.