3M™ Medical Tape 4576 for Long-Term Stick-to-Skin Applications
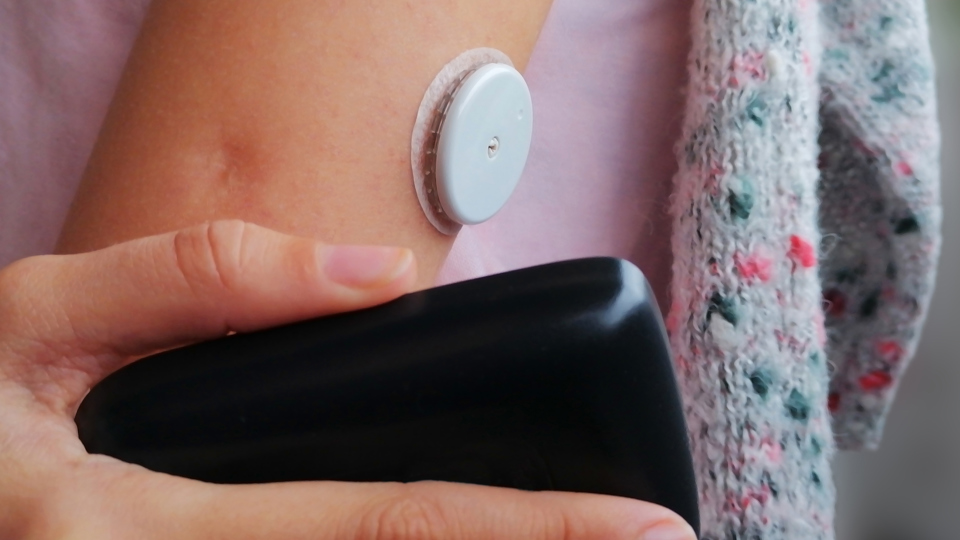
3M™ Develops New Longer-Term Wear Skin Contact Adhesive Tape
3M™ has been sticking things to the skin for around 55 years - infection prevention, IV placement, even electrode attachment. Most of those products, however, are designed to hold anywhere from only a few hours to a few days.
Wearable medical devices like continuous glucose monitors and drug delivery systems require a new type of adhesive, one that can remain on the skin for an extended period. the 3M Medical Solutions Division saw the unmet need and developed a new long-term wear adhesive tape to meet it.
We recently spoke with Audrey Sherman, Division Scientist, and Del Lawson, Medical Materials & Technologies Laboratory Manager, both of the 3M™ Medical Solutions Division, to discuss the development of their new extended wear medical tape - 3M 4576 - and the challenges they faced during the development of such a game-changing medical adhesive tape.
If you're ready to learn more about the new 3M 4576 extended-wear medical tape and the story of its development, let's get started.
Stick-to-Skin Adhesive Tapes - Demand for Longer Wear Duration Increasing
3M™ offers several products that meet a 10-14 day wear duration, including 4075, 4076, and 4077. However, they recognized the wearables market is rapidly moving towards even longer wear times and set out to meet the need for a stick-to-skin adhesive that stayed in place beyond the 10-14 days of their existing product line.
“We had to go back to the drawing board and start over. We went all in on a particular set of formulations with some great science behind it, and feel confident that this new product meets the needs of customers currently and into the next generation of products,” said Lawson.
3M™ Extended Wear Adhesive Tape 4576: Development Hurdles
3M™ faced three significant hurdles during the development of their new extended wear adhesive, 3M™ Spunlace Extended Wear Adhesive Tape on Liner, 4576:
1 - Into the Unknown
Developing an adhesive that would stick to the skin for longer than 14 days was uncharted territory for 3M™. Scientists wondered if it was even possible. Asking themselves questions like "How far can we push wear duration?" and "What happens when you keep something on the skin for that long?"
“We had to find a formulation that would have enough adhesive to grip and hang on for up to 21-days yet
remove cleanly and not leave any adverse effects on the user,” said Sherman.
2 - Meeting Expected Wear Duration
The adhesive must stay bonded for the expected wear duration. Medical devices are not something that you pick up at the drugstore. They require a prescription. If the medical device doesn’t stick for the number of days that the doctor, pharmacist, and device maker propose, it is like standing at the sink and dropping half a bottle of pills down the drain. Just like running out of pills, if the device pops off early, patients are left in a bind trying to figure out how to manage the gap before getting a refill.
3 - A Global Crisis
An atypical development hurdle encountered was the COVID-19 pandemic. It was challenging to develop an extended-wear skin-contact adhesive without trying it on healthy human skin.
“During the height of the pandemic, we could not even be in a laboratory together, much less get clinicians and subjects together to test on humans. So, we did extensive bench testing in the laboratory to try and sort out what would happen and offer some predictability of results once human testing began,” said Sherman.
Skin Contact Adhesive Tape - Challenges
The skin is unlike any other substrate. Skin contact adhesives must be able to move and flex with the body, withstand moisture and sweat, and do no harm when removed.
End-user demographics such as age, race, gender, body type, body hair, activity level, and patient health can all impact the material selection and adhesive performance.
“We have to be very careful about the ingredients that go into these products. We do a lot of compatibility testing to ensure we don’t cause any adverse or allergic reactions. It is important to test worldwide and at various times of the year. Geography, climate, and genetics all play a large role in skin properties,” said Lawson.
Wear performance also depends on the design of the device, including its size, weight, and rigidity.
“We are not yet into flexible electronics that bend and move like skin. Since most wearable devices are still rigid, you need to rely on the layer between the skin and the device to hold and absorb that stress.
It is a gradient of stress from the skin up to the rigid wearable device. If you don’t consider that, the device can pop or lift off, leading to failure. You need an adhesive skirt that sticks out beyond the edge of the device to help manage that stress,” said Sherman.
Stick-to-Skin Adhesive Tapes - Back to Basics
3M™ went back to basics on pressure-sensitive adhesives to push past the current 10-14 day wear limitations. Fifty-five years of science and innovation gave them a solid foundation to build upon.
“We know a lot about how to manipulate adhesives on different substrates. I like to say that in the laboratory, we torture polymers. We do this to ensure that when we get to the skin, we have an adhesive that meets the required wear duration without causing trauma when removed,” said Sherman.
Each layer of a wearable device has to function together as a cohesive unit. Individual layers can interact with each other and impact performance. The best way to learn how materials perform is through prototype and testing.
Building early concepts and putting them through rigorous testing ensure you do not encounter unforeseen interactions or consequences that might cause adverse skin reactions.
“Design engineers have to be paranoid and think of all the different things that can go wrong so that you can test and ensure that nothing was missed,” said Lawson.
Pushing the Limits: 21-Day Wear Duration
After all the research, innovation, and testing, 3M™ introduced their Spunlace Extended Wear Adhesive Tape on Liner, 4576. 3M™ 4576 is an acrylate-based adhesive that provides excellent adhesion to the skin while remaining flexible and conformable.
According to 3M™, here are some suggested applications:
- Extended wear medical and retail applications requiring secure attachment to skin for up to 21 days
- Can be used for attaching the finished device to the skin
- Excellent adhesion to low surface energy materials
- Material and/or technology for health care, retail, or medical device construction
Visit the 3M™ website to learn more about the new 3M™ Medical Tape 4576, or check out FindMyAdhesive.com for help selecting the right adhesive for your next medical device project.
Beyond 21 Days: Is it Possible?
“People often ask us how far can wear duration be extended. I don’t think we know yet. Every 14 days, your skin replenishes itself, and a new layer rises to the top, so it is logical to assume there is some type of limit there.
It comes down to how long you can have something on the skin that meets the do no harm criteria. So, I don’t think we are willing to say there is a limit yet. There probably will be one at some point, but we will continue to push that boundary,” said Lawson.
Converting Concepts into Reality - From Roll Goods to Finished Parts
Long-term wearable medical devices rely on pressure-sensitive tapes to hold the device together and stick to the patient's skin. Most of these adhesive tapes are produced in large, bulk rolls, but the end-user or device customer rarely requires it in this format. That’s where JBC Technologies comes in - a skilled material converter and precision die cutter.
Here are four ways JBC Technologies can help:
- Rapid Prototyping: Pair adhesives with foams, felts, flocks, nonwovens, films, or foils. Test several materials for the same part and perform fit, form, and function tests.
- High Quality, High Volume Production: We can produce parts quickly and cost-effectively with converting services that include rotary and flatbed die-cutting and lamination.
- Optimized Part Presentation: Save time and eliminate inefficiencies with part optimization processes, including kiss-cutting, butt-cutting, island placement, through-cutting, and release liner pull tabs.
- Fewer Resource Constraints: Maximize financial and human resources by outsourcing to a converter utilizing the best equipment and highly skilled operators for each application.
Check out our blog Four Benefits of Working with a Flexible Materials Converter, to learn more.
JBC + 3M™ = Value-Added Solutions
As a 3M Preferred Converter, JBC works closely with 3M to navigate the ins and outs of skin science. Assistance with adhesive selection is just one of the many value-added solutions JBC offers to help our medical device customers improve quality, reduce costs, and increase efficiency.
Our engineers and technicians have over a century of combined expertise in material selection and product design knowledge. Contact us today to learn more about how our custom solutions can help you convert your design concepts into reality.