Do You Really Need a Silicone Pressure-Sensitive Adhesive?
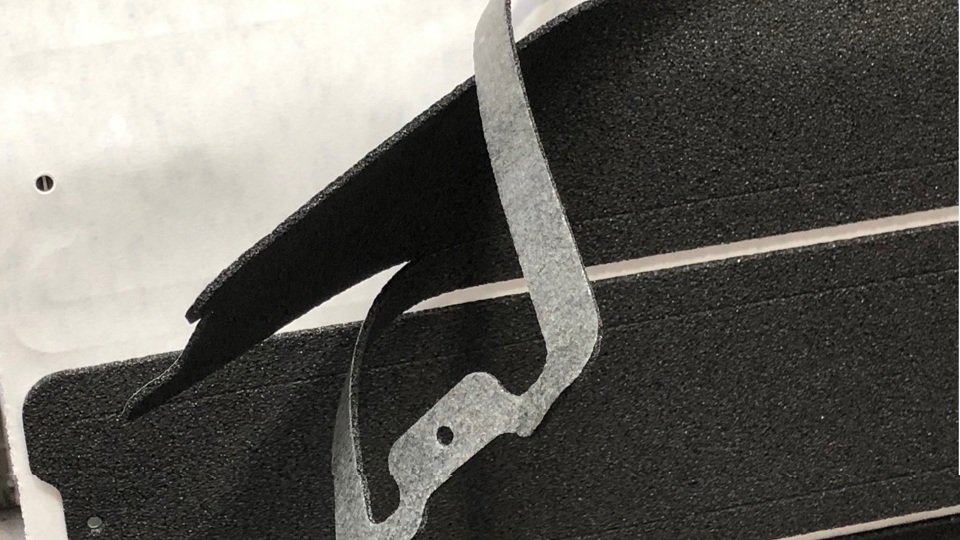
Most pressure-sensitive adhesives (PSAs) for die cut products use rubber, acrylic, or silicone chemistries. Acrylic PSAs provide the widest range of performance, but they can’t match silicone adhesives in terms of high-temperature resistance. Thanks to advances in acrylic chemistry, however, some acrylic PSAs provide excellent performance at temperatures as high as 350° F. Silicone-based PSAs withstand temperatures up to 500° F, but they cost more.
Balancing Application Requirements
For engineers, balancing all of the application requirements during PSA selection can be challenging. Material cost and temperature resistance are important, but there are usually other factors to consider, too. For example, silicone-based PSAs provide resistance to moisture, weathering, ultraviolet (UV) light, and some chemicals. They also have good conformability, provide excellent electrical insulation, and offer some sound and vibration dampening.
The substrate material to which a PSA must adhere is also a key consideration. Traditional acrylic PSAs adhere well to aluminum, steel, tin, and glass. Newer, all-acrylic PSAs support reliable attachment to non-metallic materials such as polyethylene (PP) and polypropylene (PE), plastics with a low surface energy. For engineers then, understanding the relationship between adhesive chemistry, surface energy, and substrate material is also part of PSA selection.
Surface Energy and Substrate Type
Surface energy is a measure of the excess energy at the surface (as opposed to within the bulk) of a solid material. Different substrate materials have different amounts of surface energy, and this affects “wetting out”, an industry term that describes how well an adhesive spreads. If an adhesive doesn’t “wet” properly, a strong bond between the PSA and the substrate surface won’t form. To ensure proper “wetting”, an adhesive’s surface energy should be equal to or lower than the surface energy of the substrate.
In layman’s terms, you can think of surface energy and “wetting out” in terms of washing your car. If your car’s hood is freshly-waxed, water beads up and rolls off. It’s similar to what happens when a PSA with a higher surface energy is laminated to a substrate with a lower surface energy. Instead of “wetting out” the entire surface, the PSA beads up and rolls off. Now let’s return to our car analogy. If you spray water onto a hood that’s unwaxed, the water spreads out and remains as a thin film across the entire surface. The unwaxed surface has a higher surface energy, and grips and holds the lower surface energy water.
Again, unless a PSA can “wet out” properly, a full bond isn’t achievable. Yet surface energy is about more than just the substrate type, as our example with waxed and unwaxed surfaces indicates.
Surface Treatments and Adhesive Strength
With PSAs, surface condition must be considered since a smooth, non-porous surface may not readily support adhesion. PSAs usually don’t require extensive surface preparation, but surface coatings and fillers can affect adhesive strength. For example, painted aluminum panels or plasticized polyvinyl chloride (PVC) may not bond as readily as unpainted aluminum panels or regular PVC.
Applying primers and adhesion promoters to substrates can support the use of PSAs with low-surface energy materials. Manufacturers of materials such as plastic films also use corona, plasma, and flame treatments to increase surface energy and “wetting out”. Many substrates that are primed or treated are available, but additional surface preparation may be required. For example, a surface that’s covered in heavy oils or greases may require the use of a degreaser or solvent-based cleaner before a PSA is applied.
PSAs for Die Cut Products
Do you need help selecting PSAs for die cut product? JBC Technologies has extensive die cutting experience, the best converting equipment in the business, and the right combination of application knowledge and technical expertise. To learn more, contact us today.