Part Design Tips to Optimize Your Custom Die-Cutting Project
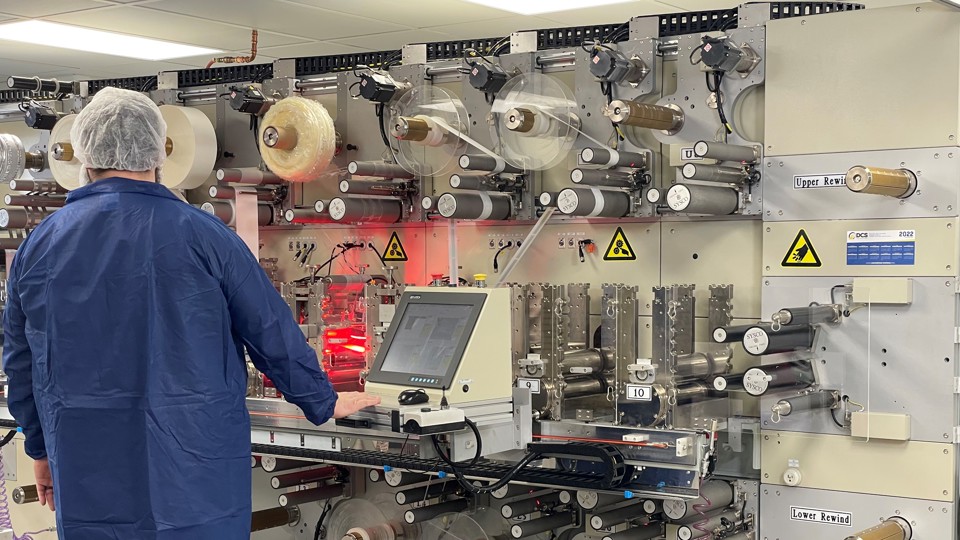
8 Things to Keep in Mind When Designing Your Die-Cut Part
JBC’s technical sales and engineering teams have hundreds of years of combined experience helping customers in industries as diverse as automotive, appliance, electronics, energy storage, medical, and aerospace take their gasket, seal, bonding tape, heat shield, and other die cut components from concept into reality.
As an organization that prides itself on Continuous Improvement, “Lessons Learned” is a phrase that is ingrained into our culture. Today, we’re here to share some lessons learned about design for manufacturability, cost competitiveness, and post-die-cut process production efficiency.
1 - Material Selection
When selecting materials for your die-cut product, ensure that substrate and environment factor heavily into your decision. This is particularly important for adhesives because things like the surface energy of the substrate, the application method, and more can play a big factor in the success or failure of the part. Read A Guide to Preventing Pressure Sensitive Adhesive Failure and Bonding Low Surface Energy Materials for more detail.
But adhesives aren’t the only material you need to think about. With so many options out on the market, there is often more than one option that will accomplish your objective. If your design isn’t locked in, take advantage of your converter’s expertise and expansive supplier network to help you narrow down your options.
Also, don’t get hung up on “the way we always do it.” For one thing, with all the material science expertise out there, material manufacturers keep coming out with new and better products. For another thing, there can be a tendency to over-engineer (and consequently overspend). There are many times that lower-cost materials can work as well or better as the higher-cost alternatives.
A few rules of thumb...
|
2 - Part Design /Design for Manufacturability
Unfortunately, the terms “design” and “design for manufacturability” are not always synonymous. When possible, engage your converter early in the process and keep an open mind if and when they offer suggestions for improved processing. The result is typically a win-win: a less expensive part, that is less prone to quality concerns.
A few rules of thumb...
|
3 - Design Tolerances
Die-cutting tolerances are driven by a combination of factors that include the size, shape, and internal features of the part, the production method, and the type of material. And, if there is one thing that is challenging about flexible materials converting, it is that there are so many different materials that we work with day in and day out that react to the die-cutting process quite differently.
For example, while plastics and other firm materials are quite rigid and will rarely change shape during the cutting process, most foams and foam tapes will stretch or compress from one degree to another. While JBC has production techniques that can minimize beveling and apple-coring, with some materials it cannot be avoided entirely. It's also important to factor in the environmental conditions in which the parts will be shipped and stored at your facility prior to being used in production, as some materials can expand or contract with changes in humidity or temperature. |
A few rules of thumb…
|
4 - Part Presentation
When you work with a die-cut solutions provider like JBC Technologies, you’ll often hear terms like pull tab, kiss cut, gapped, through cut, butt cut, on a roll, slugs removed, back-scored, perforated, etc. Basically, these are all terms that explain in what form factor we can deliver the part.
While part presentation might seem like a simple thing (after all a part is a part, right?), it is not something to be taken too lightly. As this case study illustrates, the WAY we deliver the parts can have a significant impact on your plant’s workflow and efficiency. As indicated in the case study, many of our customers prefer their parts supplied on rolls with all waste and holes/cut-outs removed, and when we fabricate parts out of acrylic foam tapes, customers more often than not request a pull tab for easy liner removal. | ![]() |
Your process may be different, however, so be sure to share your application method with your technical sales representative.
A few rules of thumb
|
5 - Prototyping
Testing and Prototyping: Conduct thorough testing and prototyping to ensure the die-cut parts meet performance requirements before mass production. This helps in identifying any design flaws early on. JBC has multiple ways to create prototype parts without the need for expensive tooling using our digital cutting capabilities.
6 - Design for Automation
Once we know you’ll be processing the parts we make via automation, there are several things we can do to set you up for success, some as simple as using a polyester liner in lieu of a paper liner so you don’t need to be concerned about tearing. We’ll also want to incorporate a visual or inline inspection process for removing misaligned or misoriented parts.
There are other things that will require a deeper conversation for us to get right. For example, if you are using a camera for visual part detection, you’ll want to consider the similarities between the die-cut material color and the substrate color if cameras will be used to visually detect the presence of a part – as an example, a black foam gasket on black ABS can be tough for cameras to see, so a different material choice may be recommended.
Did you know? JBC Technologies can help you shorten your supply chain by taking on some of the automated assembly work. Need a die-cut acrylic foam tape added to a plastic clip? Or a foam washer applied to an injection molded part? Just ask. | ![]() |
7 - Material Yield
Because raw materials are a driving factor in the cost of the majority of parts that we fabricate at JBC Technologies, it is always best when we are able to minimize waste. If you have any flexibility in design and cost is a factor, please advise your technical sales rep as he or she should be able to offer recommendations for improved material yield.
Practical Tip:Consider cutting very large parts in pieces if possible, to allow for the best material utilization. As an example, a 34" part cut out of 54" wide material = 20" scrap. Cut the parts in half to 17" and now it’s a multiple of 54" |
8 - Kitting
Avoid family dies or designing dies as a set unless the parts are always purchased and sold as a kit in an aftermarket application. Handed parts are usually assembled at different workstations and are rarely used at a similar take rate. Avoid putting dissimilar parts in a common tool to save a few tooling dollars. It will cost in the long run.
Contact JBC directly, for more tips on design for die-cut manufacturability…
The list of things we could cover is extensive, so we’ll cut it off before we make things overly complicated. If you take anything away from this post, however, it should be that you should always consider consulting your converter as early in the design phase of your part as possible, as we can add value that extends far beyond the actual process of producing your parts.
For over 35 years, we've been helping our customers improve their products with custom die-cut solutions. Custom die-cut solutions from JBC Technologies can be found in nearly every industry, from automotive and medical to HVAC and appliances.
We're an ISO 9001, IATF 16949 Certified manufacturer and a 3M Preferred Converter.
Contact us today!