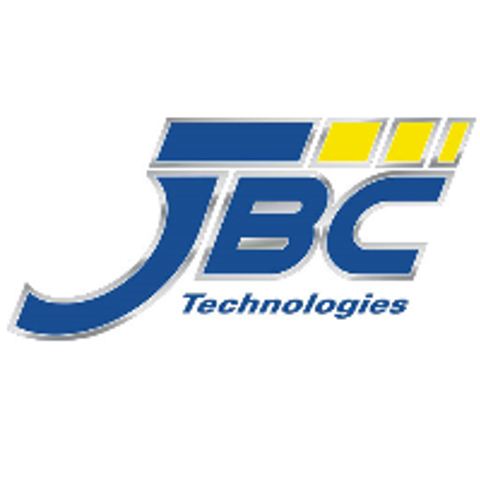
JBC Technologies
Explore insights and expertise on material science, die-cutting, and engineering solutions in JBC Technologies' blog, authored by their industry experts.
Explore insights and expertise on material science, die-cutting, and engineering solutions in JBC Technologies' blog, authored by their industry experts.
In this edition of JBC's Faces of JBC series, we get to know Eric Lee -- a Material Handler at JBC's Madison Wisconsin facility.
Welcome to the latest edition of Faces of JBC. This blog series highlights the team members who make JBC one of the country's leading die-cutting and material-converting experts. Get to know the names behind the functions and the faces and stories behind the names. Today, we feature a member of Team JBC-North Ridgeville. Say hello to JBC-North Ridgeville Production Associate Gwen Jackson.
JBC Technologies announces it has obtained IATF 16949:2016 accreditation for its North Ridgeville, Ohio manufacturing site. The IATF 16949 certification is a comprehensive quality management standard designed to help organizations improve quality, increase efficiency, and reduce costs throughout the automotive supply chain.
Selecting a die cutting partner should involve considerations beyond price, quality and delivery. Today, the most sophisticated die cut suppliers offer value in the areas of product design, delivery systems, quality and product integration. Learn more here.
We're excited to announce a new addition to our precision die-cutting family - a 10-station high-speed rotary die-cutting press from Dorey Converting Systems (DCS). At JBC Technologies we continue to expand and enhance our precision capabilities so that we can better serve our customers and improve our high-performance and tight-tolerance production. The new DCS die-cutting press will be...
Die-cut seal or gasket material selection should always begin with an assessment of the application in which the finished part will be utilized and there are several common factors that should come into play as part of that evaluation.