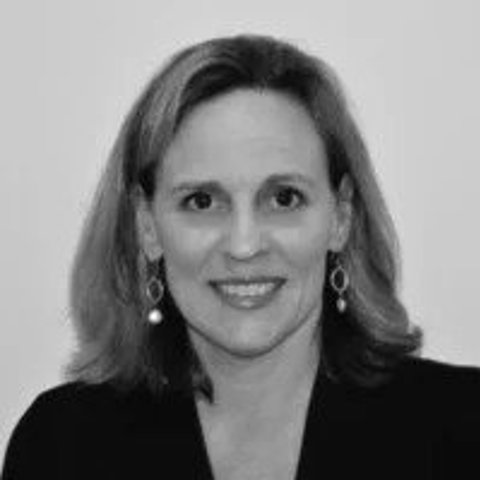
Kate Gluck
Kate Gluck is the Vice President of Business Development at JBC Technologies.
Kate Gluck is the Vice President of Business Development at JBC Technologies.
Today we are here to shine the spotlight on a specialty insulation material that we have been converting into custom die-cut solutions for quite some time now – Superwool, by Morgan Advanced Materials. Superwool is an engineered low biopersistent alkaline earth silicate (AES) insulation solution developed as an alternative to traditional refractory ceramic (RCF) or fiberglass materials.
Advances in medical device design are driving lighter, smaller, more user-friendly stick-to-skin devices that can be used in at-home settings as well as in a hospital or physician’s office. But while they are easy to use from an end-user standpoint, they are not always simple to design and fabricate. Many “patches” are actually complex multi-layer material laminations that require significant thought on material selection and design for manufacturability. This post examines 8 key things to consider when designing a multi-layered stick-to-skin product.
Neograf’s eGraf® SpreaderShield™ is steadily gaining traction as a material of choice within the EV space. Today’s post, which features insights and input from Bret Trimmer, Applications Engineering Manager at NeoGraf Solutions, LLC, will highlight the five benefits of using a layer of die-cut flexible graphite within an electric vehicle battery—at the pack level, the module level, and in between the battery cells themselves.
When designing a stick-to-skin die-cut adhesive patch for long-term wear medical or health and beauty applications, it is important to select a carrier that balances breathability and moisture transmission with an adhesive’s ability to seal out contaminants. Materials with the right balance will stay adhered to the skin while minimizing moisture build-up, improving patient comfort, and reducing the risk of infection. This article examines which carriers offer higher moisture vapor transmission rate (MVTR) levels for long-term wear stick-to-skin applications and how pattern-coated adhesives can benefit MVTR.
Within the world of the EV battery, there are many applications for custom die-cut materials, in particular, tapes and adhesives. What lies ahead will be an educational journey through the many benefits one might see when choosing to use die-cut pressure-sensitive adhesives and tapes instead of mechanical fasteners and liquid adhesives and sealants in an EV battery application.
How do you select the right pressure-sensitive adhesive for your stick-to-skin application? Balancing adhesion strength, breathability, conformability, and removability, along with end-use wear time needs - it can be tricky. Short-term wear stick-to-skin adhesives may need but a few minutes or a few days to be effective while long-term wear could mean as much as a month. Let's see some of the different applications for short- and long-term wear stick-to-skin adhesives and take a look at what medical device design engineers should consider when selecting carriers and adhesives for on-body applications.